Ready to turn insight into action?
We help organisations transform ideas into measurable results with strategies that work in the real world. Let’s talk about how we can solve your most complex supply chain challenges.
A warehouse is more than just an empty space for storing stock — it's a critical hub for managing inventory, fulfilling orders, and ensuring the smooth operation of supply chain activities. Every square foot counts in the complex supply chain environment.
When considering renting or purchasing a warehouse, you should look beyond storage capacity. Also, evaluate how well you can conduct business operations in the given space. Accessibility, space utilisation, and workflow efficiency are other pivotal factors in this decision.
A well-thought-out warehouse layout is key to streamlining processes, enhancing productivity, and effectively managing the warehouse and all related operations. Delve into the fundamental principles of warehouse layout planning to design a productive warehouse.
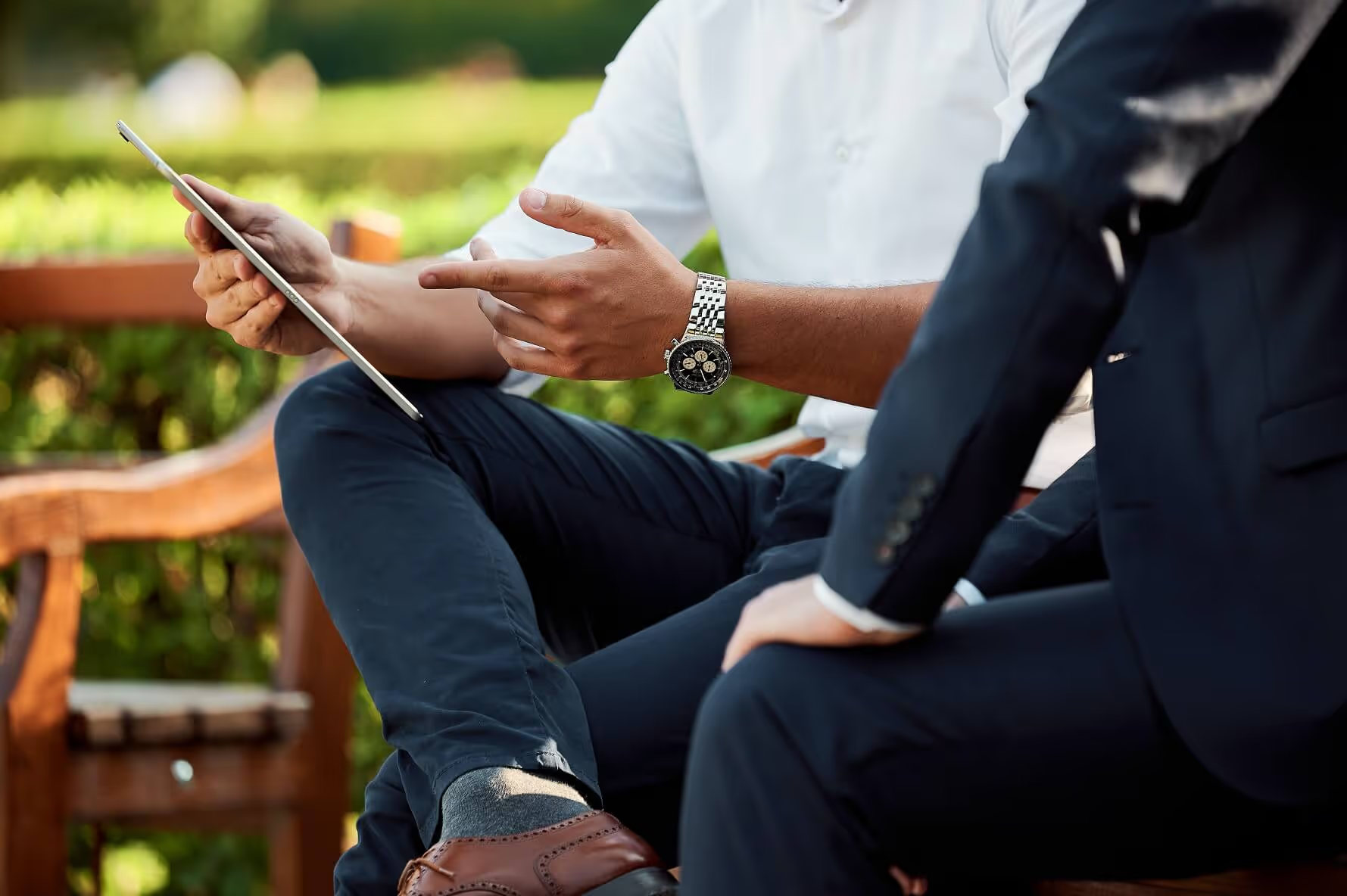
The Difference Well-Designed Warehouses Make
Planning a warehouse layout is a significant investment of time, energy, and financial resources. When managed well, it yields long-term benefits far outweighing the initial costs. The effort put into planning and designing an optimal layout pays dividends in the form of a streamlined and more effective operation.
A warehouse design tailored to align with your company's operations and needs simplifies work processes, benefiting the entire team. With a layout that supports your specific operational flow, you can anticipate a smoother, more efficient work environment. This results in fewer disruptions to minor and major operations, increasing consistency and reliability in your business activities.
A warehouse is an ecosystem that supports and enhances your business operations. Paying attention, even to the finest details, can create a space adaptable for future growth and changes.
Design Principles of Warehouse Layout Planning
Creating warehouse layouts is inherently flexible. While there is no one-size-fits-all blueprint, certain proven and tested principles of warehouse layout planning can guide you in designing a space that works for you.
- Maximising Space Utilisation: One of the primary principles is the efficient use of available space. It involves strategically organising storage areas, aisles, and workstations to maximise storage capacity and minimise wasted space. It's essential to consider both vertical and horizontal space, utilising shelving and stacking methods that make the most of the warehouse's footprint.
- Optimising Workflow: A well-planned warehouse layout facilitates smooth workflow. Opt for a space that allows a logical and efficient flow of materials and employees through the facility. Placement of goods should be based on the frequency of access and the sequence of operations, from receiving to shipping, to minimise movement and handling time.
- Flexibility and Scalability: A flexible warehouse layout can adapt to changing business needs and market demands. You may implement scalable storage solutions and modular designs that can quickly reconfigure as inventory levels and operational requirements evolve.
- Safety Considerations: Safety is paramount in warehouse design. Layouts should ensure clear visibility, minimise the risk of accidents, and comply with regulatory safety standards. Ensure adequate spacing for safe movement, attach proper signage, and seek ergonomic solutions to prevent workplace injuries.
- Technology Integration: warehouses benefit greatly from integrating modern technology into their layout. Innovative upgrades can optimise picking processes, inventory management, and overall operational efficiency.
Things to Consider When Creating a Warehouse Layout
Besides familiarising yourself with popular design principles, it is also helpful to be keen on the factors that critically affect the feasibility of a specific blueprint. These components may help refine your plans for warehouse design:
- Product Profile: A company's product profile can dictate storage requirements and levels of automation. For example, bulky items might need larger shelving spaces, while fragile items require secure, cushioned storage. An automated retrieval system might be ideal for highly standardised and durable products, enhancing efficiency and reducing manual handling. Conversely, products that require careful handling might necessitate more manual processes.
- Demand Profile: Understanding a company's demand profile is crucial for effective warehouse layout planning. Demand often peaks during certain seasons, requiring a layout accommodating fluctuations. Easy access to high-demand items is essential to expedite order processing during peak seasons. You must strategically position fast-moving SKUs to minimise picking time and improve workflow efficiency. In comparison, you can store slow-moving SKUs in less accessible areas.
- Number of Workers: The size of your workforce impacts the layout design, too. More workers necessitate adequate space for safe and efficient movement. The layout should promote a systemic workflow that minimises bottlenecks and allows workers to perform tasks without hindrance.
- Location: The geographical location of your warehouse can influence its layout. Factors like climate, local regulations, and proximity to transport links should be considered. For example, in areas prone to severe weather, your layout must prioritise protective storage solutions. In contrast, warehouses in urban neighbourhoods should focus on maximising vertical space due to limited ground area.
- Capacity Requirements: Consider your business' capacity requirements when designing a warehouse layout to ensure efficient storage and operations. Adequate space planning is essential to accommodate inventory needs, equipment, and future growth, optimising the warehouse's functionality and minimising disruptions.
More Ways to Make a Warehouse Efficient
Designing a blueprint tailored to a business's specifications is crucial in creating an efficient warehouse. However, the enhancements do not end there — fine-tune some of its aspects once the design materialises into a solid structure.
To make a warehouse more efficient, consider these suggestions:
- Warehouse Automation: Implement automated sorting, picking, and packing systems. You can reduce manual errors, speed up processes, and significantly increase productivity.
- Regular Training for Staff: Ensure staff are well-trained and updated on the latest warehouse operations and safety protocols.
- Continuous Improvement Process: Regularly assess and update the warehouse layout and processes based on changing business needs and technological advancements.
- Energy Efficiency Measures: Adopt energy-efficient lighting and machinery. This initiative reduces operational costs and contributes to a more sustainable environment.
These enhancements, especially when coupled with warehouse automation, can significantly improve the efficiency and functionality of your warehouse, leading to a smoother flow of operations and a better bottom line.
What is warehouse inventory management (WMS)?
After selecting or building a location with your ideal warehouse configurations, it's time to learn how to manage the space better. Warehouse inventory management involves overseeing the warehouse's storage, handling, and tracking of goods. It includes managing stock levels, ensuring accurate record-keeping, and coordinating the movement of goods in and out of the warehouse.
Effective WMS is vital to your business, particularly regarding supply chain management. It ensures that inventory is stored efficiently, minimises the risk of stockouts or overstocking, and facilitates timely order fulfilment. A good system directly affects the efficiency of your supply chain, impacting everything from production schedules to customer satisfaction.
Choosing the Warehouse Management System for You
Nowadays, there are countless options for ‘off the shelf’ WMS. These systems come in different variants, catering to a multitude of business sizes and types. However, for those with specific requirements, there's also the option to customise a system to suit your unique demands.
Regardless of the type of WMS you choose, trace. is here to support you. We can help you understand key gaps and opportunities, define your functional requirements, go to market and select a vendor as well as implement the solution. We leverage our tools and expertise to respond to the needs of modern businesses. Our team is committed to working closely with you, understanding your challenges and goals, and addressing your growing needs. trace. is your partner in optimising warehouse operations.
Ready to turn insight into action?
We help organisations transform ideas into measurable results with strategies that work in the real world. Let’s talk about how we can solve your most complex supply chain challenges.