Revolutionise Your Supply Chain with Effective KPIs

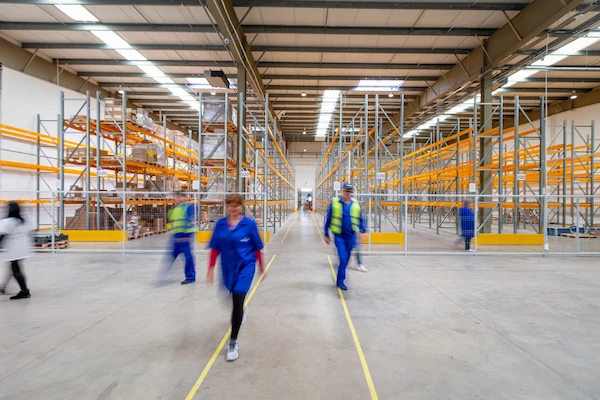
KPI & Supply Chain Organisational Design Solutions
For supply chains to deliver maximum efficiency, service performance, and cost competitiveness, they must be supported by the right organisational structure, workforce capability, and performance measurement framework. However, many organisations struggle with:
❌ Misaligned organisational structures leading to inefficiencies
❌ Unclear roles and responsibilities causing operational bottlenecks
❌ Poor visibility into performance metrics due to weak KPIs
❌ Lack of accountability in decision-making within supply chain teams
At Trace Consultants, we help organisations design and optimise their supply chain structures and KPIs to ensure they operate with agility, efficiency, and strategic alignment. Our expertise spans retail, FMCG, manufacturing, healthcare, government, and logistics, ensuring solutions that are tailored to industry challenges.
Why Organisational Design & KPIs Matter in Supply Chain
A well-structured supply chain organisation enables businesses to:
✅ Improve decision-making speed and accuracy
✅ Enhance collaboration between supply chain, procurement, and operations
✅ Reduce costs by eliminating inefficiencies and redundant roles
✅ Align roles and responsibilities with business goals and customer needs
✅ Establish clear performance accountability with data-driven KPIs
By designing an optimal supply chain operating model, organisations can ensure that people, processes, and technology work together seamlessly to achieve business objectives.
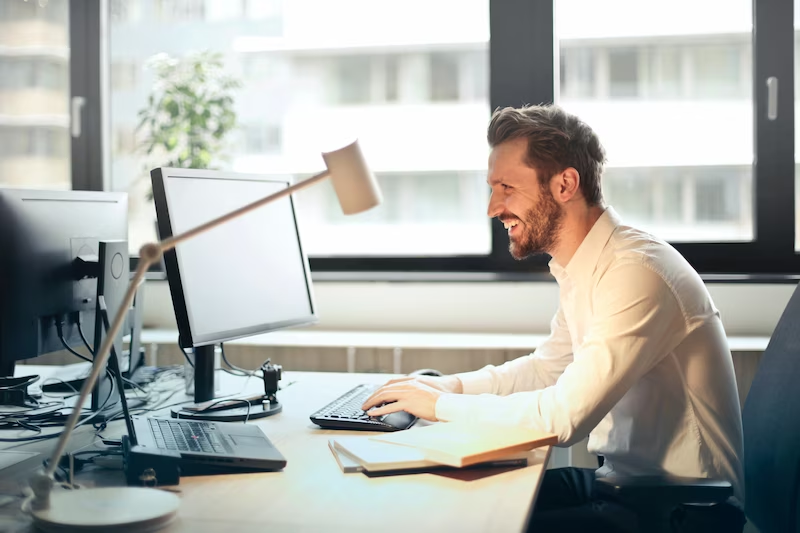
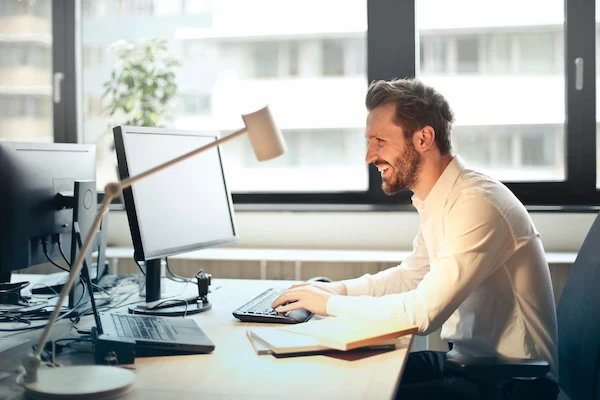
.avif)
.avif)
To complement a purposeful organisation structure, leading supply chains have clear and aligned policies and KPIs to provide focus, guide behaviour and drive accountability for supply chain and organisational performance.
Our KPI & Supply Chain Organisational Design Services
1. Supply Chain Organisational Structure Design
Many supply chain teams evolve organically rather than strategically, leading to role duplication, misalignment, and operational inefficiencies. We help organisations:
✔ Redesign their supply chain organisation structure to match business objectives
✔ Define clear roles and responsibilities to reduce operational bottlenecks
✔ Optimise reporting lines and governance frameworks for faster decision-making
✔ Implement best practices in workforce planning to improve agility and resilience
Common Organisational Design Challenges We Solve:
- Decentralised vs. Centralised Models: Determining whether supply chain decision-making should be centralised for efficiency or decentralised for agility
- Cross-Functional Integration: Aligning supply chain, procurement, sales, and operations to improve responsiveness
- Global vs. Regional vs. Local Structures: Optimising teams to balance cost efficiency, standardisation, and local market needs
-
2. KPI Development & Performance Management Frameworks
Many organisations struggle with measuring and improving supply chain performance due to unclear or misaligned KPIs. We develop data-driven KPI frameworks to ensure:
✔ Clear visibility into supply chain performance at all levels
✔ Alignment of KPIs with business objectives (cost, service, sustainability, resilience)
✔ Integration of financial and operational metrics for end-to-end visibility
✔ Real-time monitoring and reporting for proactive decision-makingKey KPI Areas We Optimise:
📊 Supply Chain Efficiency KPIs: Cost per order, inventory turnover, supply chain cost-to-revenue ratio
📦 Warehouse & Logistics KPIs: Order accuracy, fulfilment speed, DIFOT (Delivered In Full, On Time), warehouse utilisation
🚛 Transport & Freight KPIs: Freight cost per unit, carrier performance, carbon footprint
🔗 Procurement KPIs: Supplier performance, cost savings, contract compliance, ESG impact
📈 S&OP & Demand Planning KPIs: Forecast accuracy, demand-supply balance, stock availability
3. Supply Chain Operating Model Redesign
Many supply chain inefficiencies stem from poorly designed operating models. We work with organisations to:
✔ Redefine decision-making structures for improved agility
✔ Optimise processes for inventory, warehousing, procurement, and logistics
✔ Implement best practices in digital transformation and automation
✔ Ensure supply chain processes align with financial and customer service goals
4. Workforce Capability & Training Programs
Even the best organisational design and KPIs will fail if teams lack the right skills or tools. We help businesses:
✔ Develop workforce capability roadmaps to ensure teams have the right skills
✔ Implement training programs for supply chain leadership, planning, and execution
✔ Embed data-driven decision-making into supply chain teams
✔ Introduce digital tools and automation to enhance performance monitoring
Why Work with Trace Consultants?
Deep Supply Chain & Procurement Expertise
We have a specialist focus on supply chain and procurement, ensuring that organisational design, KPIs, and operating models are not generic but tailored to real industry challenges.
Data-Driven & Practical Approach
We combine advanced analytics, industry benchmarks, and practical implementation expertise to ensure real-world impact and measurable improvements.
Proven Track Record
We have successfully redesigned supply chain organisations, implemented KPI frameworks, and optimised operating models for businesses across retail, FMCG, manufacturing, healthcare, and logistics.
Transform Your Supply Chain Organisation & KPIs for Success
A high-performing supply chain requires the right structure, the right metrics, and the right people. Whether your organisation needs to redesign its operating model, improve KPI tracking, or optimise workforce capability, Trace Consultants provides the expertise to deliver tangible results.
Want to unlock the full potential of your supply chain organisation? Contact us today to discuss how Trace Consultants can help.
Want to work with us? Enquire today!
We pride ourselves on being Australia’s benchmark boutique advisory firm specialising in supply & service chain strategy. You can count on our expert team to provide you with robust and practical solutions to the many different factors that affect efficient supply chain management. Our consultants can help with planning operations, setting up warehouse distribution systems, workforce rostering and improving your customer experience. We pride ourselves on creating resilient and sustainable supply chain systems. Contact us to begin working on your business's supply chain strategy today.
Want to work with us? Enquire today.
As Australia's leading boutique advisory firm, we specialise in service and supply chain strategies for clients in both the private and public sectors. Setting the benchmark for excellence, our warehouse design and inventory management consultant team is dedicated to providing practical solutions that streamline your organisation's operations. Additionally, we offer comprehensive consulting services in critical areas, including resilient and sustainable business models, operational planning, warehousing distribution, organisational design KPIs, customer experience, and sustainability. Contact us today to take the first step towards developing a robust workforce planning strategy for your business.
Enquire now