Ready to turn insight into action?
We help organisations transform ideas into measurable results with strategies that work in the real world. Let’s talk about how we can solve your most complex supply chain challenges.
Interview with Shanaka Jayasinghe: The Critical Role of BOH Logistics in Designing Sustainable Hospital Facilities
In the heart of Melbourne, a new hospital is rising—a beacon of hope and a testament to modern healthcare innovation. This hospital is not just another addition to Australia's healthcare infrastructure; it is a symbol of a broader vision. As the cranes lift steel beams into place, the focus is not only on cutting-edge medical technology and patient care but also on the often-overlooked aspect of healthcare design: Back of House (BOH) logistics.
To delve into this critical aspect of hospital design, we sit down with Shanaka Jayasinghe, a partner at Trace Consultants. With years of experience in logistics and healthcare infrastructure, Jayasinghe provides invaluable insights into how BOH logistics can ensure consistency in patient care, enhance clinical outcomes, and support safe and efficient operations for both staff and patients.
Interviewer: Shanaka, thank you for joining us today. To start, could you explain why BOH logistics are so critical when designing new hospital facilities?
Shanaka Jayasinghe: Thank you for having me. BOH logistics play a crucial role in the overall functionality of a hospital. They ensure that all necessary supplies, equipment, and services are available where and when they are needed, which directly impacts patient care and clinical outcomes. Efficient BOH logistics support smooth operations, reduce waste, and improve the working environment for hospital staff, all of which are vital for maintaining high standards of healthcare.
Interviewer: That's fascinating. Could you elaborate on specific elements of BOH logistics, such as loading dock design and central stores layout, and their impact on hospital operations?
Shanaka Jayasinghe: Absolutely. The loading dock is the hospital's primary entry point for goods and supplies. Its design affects the speed and efficiency of deliveries, which in turn influences the entire supply chain. A well-designed loading dock can handle multiple deliveries simultaneously, reduce waiting times, and ensure quick turnover of supplies.
Central stores design and layout are equally important. These areas must be optimally organized to allow for easy access to supplies, efficient inventory management, and rapid restocking. Poorly designed storage areas can lead to delays, misplaced items, and even potential contamination, all of which can compromise patient care.
Interviewer: Shanaka, loading dock congestion can be a major issue in hospital logistics. How can hospitals manage and reduce congestion at their loading docks?
Shanaka Jayasinghe: Managing loading dock congestion is crucial for maintaining efficient hospital operations. Hospitals can reduce congestion through several strategies:
- Scheduling Deliveries: Implementing a scheduled delivery system ensures that suppliers arrive at staggered times, reducing bottlenecks and wait times.
- Design Optimisation: Designing the loading dock to accommodate multiple deliveries simultaneously can streamline the unloading process. This includes having enough bays and space for manoeuvring vehicles.
- Technology Integration: Using technology such as real-time tracking and automated scheduling systems can help coordinate deliveries more effectively, providing visibility and reducing overlap.
- Efficient Layout: Ensuring that the loading dock is well-organized with clear signage and designated areas for different types of deliveries can speed up the unloading process.
By adopting these measures, hospitals can significantly reduce loading dock congestion, ensuring smoother operations and timely delivery of essential supplies.
Interviewer: Space and capacity planning must be another critical aspect. How does it influence hospital logistics?
Shanaka Jayasinghe: Space and capacity planning are foundational elements of BOH logistics. Proper planning ensures that there is adequate space for all necessary functions, including storage, processing, and waste management. It also considers future growth and changes in hospital needs. By planning for flexibility and scalability, hospitals can avoid costly renovations and disruptions in the future.
Interviewer: Linen services and operating models seem like they would have a significant impact as well. Can you touch on these areas?
Shanaka Jayasinghe: Linen services are a perfect example of how BOH logistics impact daily operations. Efficient linen management ensures that clean linens are always available, which is critical for patient hygiene and infection control. This involves not only the transportation and storage of linens but also their cleaning and distribution within the hospital.
Operating models need to be tailored to the specific needs of the hospital. They dictate how services are provided, who is responsible for various tasks, and how different departments interact. A well-designed operating model ensures that all parts of the hospital work together seamlessly, which enhances efficiency and improves patient outcomes.
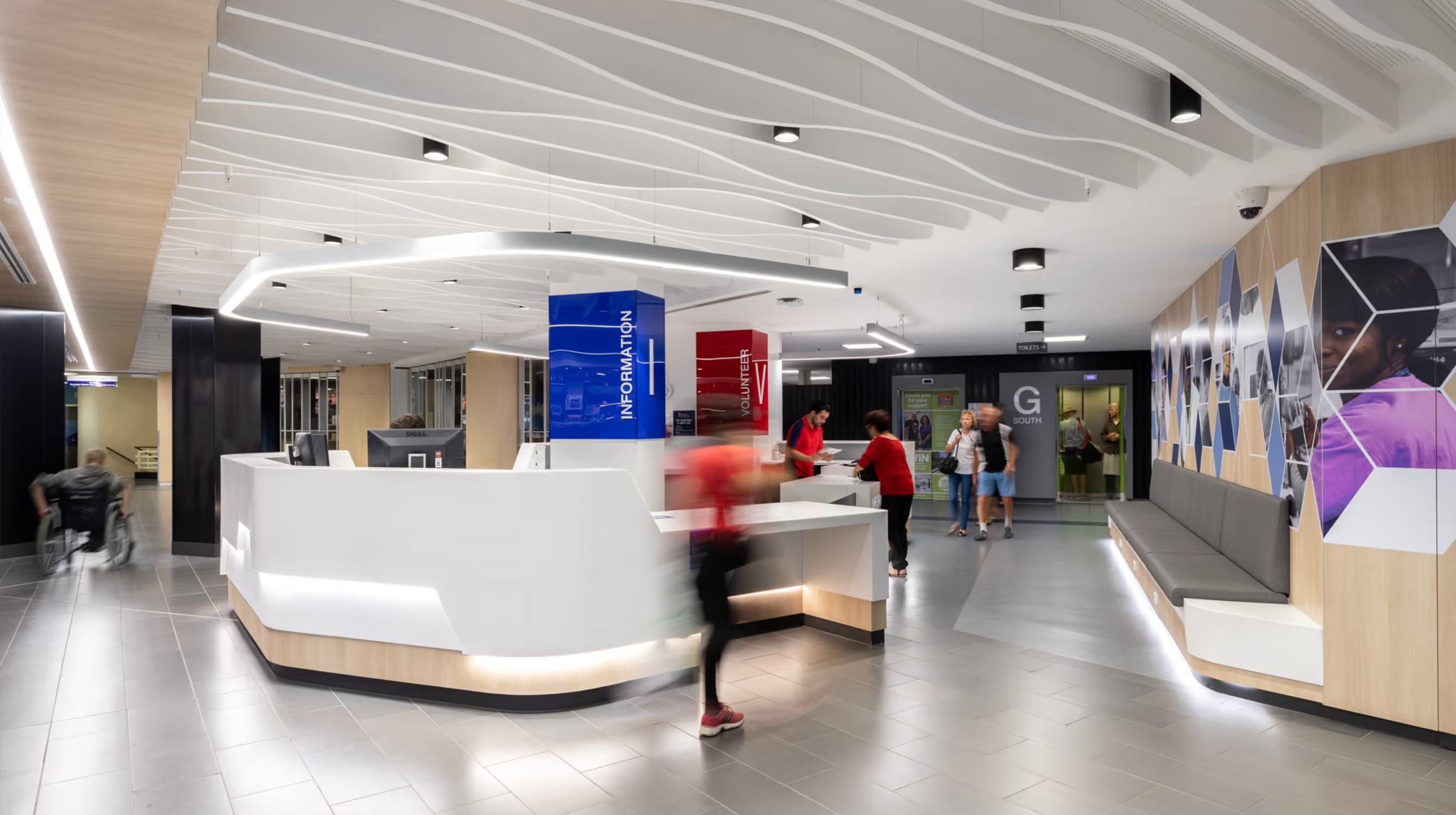
Interviewer: Production kitchens and waste management are also crucial components of BOH logistics. How do these areas contribute to the overall efficiency and sustainability of hospital operations?
Shanaka Jayasinghe: Production kitchens are responsible for preparing meals for patients, staff, and visitors. Their design must facilitate efficient food preparation, storage, and distribution while adhering to strict health and safety standards. An efficient kitchen layout can reduce food waste, improve meal delivery times, and ensure that dietary requirements are met.
Waste management is another critical area. Hospitals generate a significant amount of waste, including hazardous materials. Effective waste management systems ensure that waste is handled safely and disposed of properly, minimizing environmental impact and maintaining a safe environment for patients and staff.
Interviewer: Shanaka, clinical waste management is a significant concern for hospitals due to its potential impact on both health and the environment. Can you discuss the importance of effective clinical waste management in hospital logistics and the strategies used to handle it efficiently?
Shanaka Jayasinghe: Effective clinical waste management is crucial in hospital logistics because it directly impacts both patient safety and environmental sustainability. Hospitals generate a substantial amount of clinical waste, including sharps, infectious materials, and hazardous substances, which require careful handling and disposal to prevent contamination and infection.
Several strategies are employed to manage clinical waste efficiently:
- Segregation at Source: Waste is segregated at the point of generation into categories such as general waste, recyclable waste, and hazardous waste. This segregation helps in proper disposal and recycling, reducing the overall environmental impact.
- Proper Storage: Designated storage areas for clinical waste are essential. These areas should be secure, well-ventilated, and clearly marked to prevent unauthorized access and accidental exposure.
- Regular Collection and Disposal: Hospitals must have a robust schedule for the collection and disposal of clinical waste. This ensures that waste does not accumulate and pose a risk to patients and staff. Partnering with licensed waste disposal companies that follow stringent regulatory guidelines is crucial.
- Training and Awareness: Hospital staff must be regularly trained on proper waste management practices. This includes the correct segregation, handling, and disposal of clinical waste, as well as the use of personal protective equipment (PPE) to minimize risk.
- Use of Technology: Advanced tracking systems can monitor waste from the point of generation to its final disposal. This enhances accountability and ensures compliance with environmental regulations.
- Recycling and Minimisation: Where possible, hospitals should adopt practices that minimise waste generation and promote recycling. For example, using reusable materials and devices instead of single-use items can significantly reduce clinical waste.
By implementing these strategies, hospitals can manage clinical waste more effectively, ensuring a safer environment for patients and staff and reducing their environmental footprint.
Interviewer: How do you optimise the process from dock to ward?
Shanaka Jayasinghe: Dock to ward optimisation involves streamlining the entire supply chain from the moment goods arrive at the loading dock to their final destination within the hospital. This includes efficient inventory management, rapid restocking, and minimizing delays. Technology plays a key role in this process, with automated systems and real-time tracking ensuring that supplies are always available when needed.
Interviewer: Speaking of technology, how does it integrate with BOH logistics to enhance hospital operations?
Shanaka Jayasinghe: Technology is a game-changer for BOH logistics. Advanced software systems can manage inventory, track deliveries, and predict supply needs based on usage patterns. Automation can speed up processes and reduce human error. For example, automated guided vehicles (AGVs) can transport supplies throughout the hospital, freeing up staff to focus on patient care.
Interviewer: When reviewing infrastructure design, how important is it to consider the operating model, technology, and supply chain processes?
Shanaka Jayasinghe: It's absolutely critical. The infrastructure design should support the hospital's operating model and incorporate the latest technology and efficient supply chain processes. This holistic approach ensures that the hospital operates smoothly and efficiently, which ultimately benefits patient care and clinical outcomes. For example, designing spaces that accommodate automated systems or future technological upgrades can save time and money in the long run.
Interviewer: Finally, what advice would you give to government agencies, building authorities, and architectural design firms when planning new hospital facilities?
Shanaka Jayasinghe: My advice would be to take a comprehensive approach to planning. Consider every aspect of BOH logistics from the outset, including loading dock design, central stores layout, space and capacity planning, linen services, production kitchens, and waste management. Integrate the latest technology and ensure that the infrastructure supports efficient supply chain processes. By doing so, you will create a hospital that is not only functional and efficient but also capable of providing the highest level of care for patients.
Interviewer: Shanaka, thank you for your invaluable insights. As we look towards the future of healthcare infrastructure, it's clear that BOH logistics will play a pivotal role in shaping efficient, sustainable, and patient-centric hospital environments.
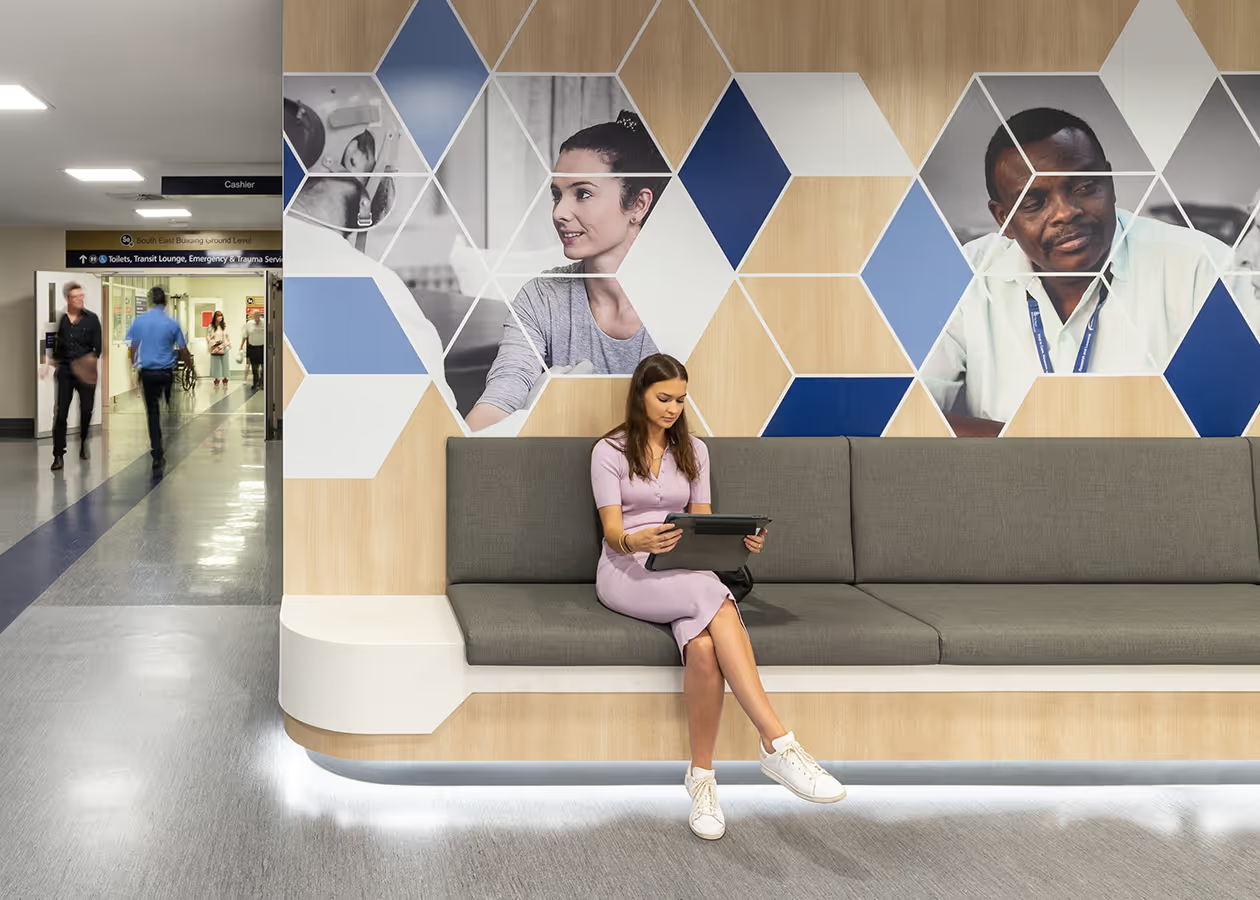
This interview provides a deep dive into the critical aspects of BOH logistics in hospital design, tailored to the needs of large Australian Government Agencies, Building Authorities, and Architectural Design Firms. By considering these logistics principles, we can build hospital facilities that ensure consistency in patient care, clinical outcomes, and efficient operations for staff and patients.
Ready to turn insight into action?
We help organisations transform ideas into measurable results with strategies that work in the real world. Let’s talk about how we can solve your most complex supply chain challenges.