Ready to turn insight into action?
We help organisations transform ideas into measurable results with strategies that work in the real world. Let’s talk about how we can solve your most complex supply chain challenges.
In the rapidly evolving world of supply chain management, the adoption of innovative technologies is crucial for maintaining a competitive edge. For Chief Information Officers (CIO) and Chief Supply Chain Officers (CSCO), low-code and no-code platforms have emerged as game-changers, enabling the development and deployment of applications quickly and efficiently without the need for extensive coding expertise. This article explores how leveraging low-code and no-code technology solutions can drive significant improvements across various supply chain functions, including demand planning, inventory management, ordering, supply planning, production scheduling, supplier management, and KPI reporting. We will also discuss how Trace Consultants can support your strategic initiatives and technology adoption.
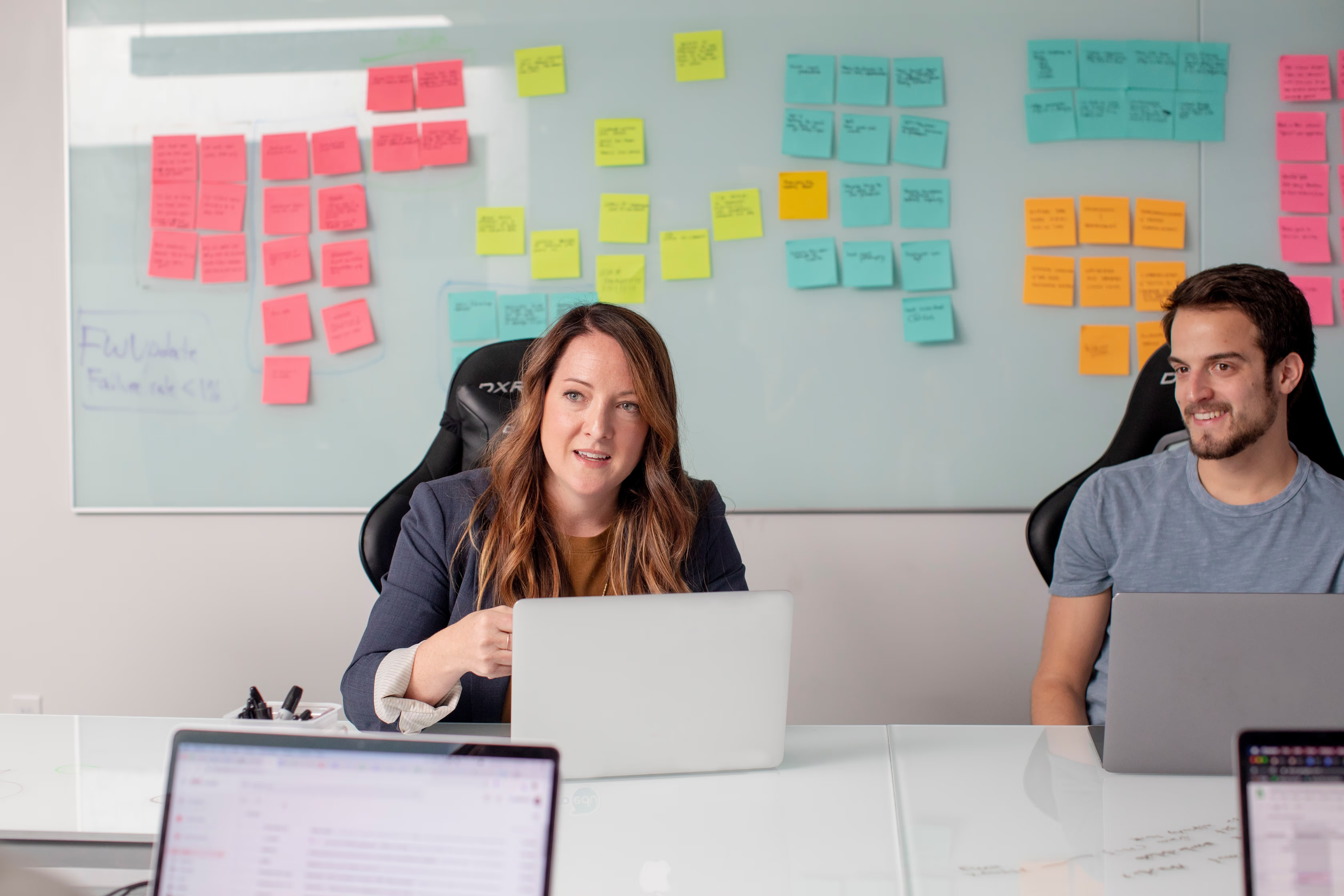
Understanding Low-Code and No-Code Technology
What are Low-Code and No-Code Platforms?
Low-code and no-code platforms are development environments that allow users to create applications with minimal hand-coding or no coding at all. These platforms provide visual interfaces, drag-and-drop features, and pre-built templates, making it easier for non-technical users to develop custom applications.
- Low-Code Platforms: These platforms require some coding knowledge but significantly reduce the amount of code needed, speeding up the development process.
- No-Code Platforms: These platforms enable users with no coding experience to build applications using visual tools and pre-configured modules.
Benefits of Low-Code and No-Code Platforms
- Speed and Agility: Rapid development and deployment of applications.
- Cost-Effective: Reduces the need for expensive developer resources.
- Flexibility: Easily adaptable to changing business needs.
- User Empowerment: Empowers business users to create and modify applications.
Applications in Supply Chain Management
1. Demand Planning
Enhancing Demand Planning with Low-Code/No-Code
Accurate demand planning is crucial for maintaining optimal inventory levels and meeting customer expectations. Low-code and no-code platforms enable CIOs and CSCOs to:
- Create Custom Demand Forecasting Models: Develop tailored forecasting models that incorporate historical data, market trends, and external factors.
- Integrate Data Sources: Seamlessly integrate data from various sources such as sales, market research, and external databases.
- Real-Time Adjustments: Quickly adjust forecasts in response to market changes or unexpected events.
Case Study: Improving Forecast Accuracy
A leading retail company used a low-code platform to develop a custom demand forecasting tool. The tool integrated sales data, seasonal trends, and market analysis, resulting in a 15% improvement in forecast accuracy and a 10% reduction in stockouts.
2. Inventory Management
Streamlining Inventory Management
Effective inventory management ensures that the right products are available at the right time. Low-code and no-code solutions help streamline inventory management by:
- Automating Inventory Tracking: Implementing automated tracking systems that update inventory levels in real-time.
- Setting Reorder Points: Creating automated alerts for reorder points to prevent stockouts and overstock situations.
- Optimising Stock Levels: Using data analytics to optimise stock levels based on demand patterns and lead times.
Case Study: Reducing Inventory Costs
A manufacturing company leveraged a no-code platform to develop an inventory management system that automated stock tracking and reorder processes. This led to a 20% reduction in inventory holding costs and a 25% decrease in stockouts.
3. Ordering
Simplifying Ordering Processes
Efficient ordering processes are essential for maintaining a smooth supply chain. Low-code and no-code platforms simplify ordering by:
- Automating Order Processing: Creating automated workflows for order processing, reducing manual errors and processing times.
- Custom Order Forms: Developing custom order forms that meet specific business needs.
- Order Status Tracking: Implementing real-time order status tracking to improve visibility and customer satisfaction.
Case Study: Enhancing Order Accuracy
A logistics company used a low-code platform to automate its order processing system. This resulted in a 30% reduction in order processing time and a 15% improvement in order accuracy.
4. Supply Planning
Optimising Supply Planning
Effective supply planning ensures that production meets demand while minimising costs. Low-code and no-code solutions enable CIOs and CSCOs to:
- Develop Custom Supply Models: Create supply planning models that incorporate production capacity, lead times, and supplier performance.
- Scenario Planning: Conduct scenario planning to evaluate the impact of different supply chain disruptions and make informed decisions.
- Collaborative Planning: Facilitate collaboration between different departments and suppliers through integrated planning tools.
Case Study: Improving Supply Chain Resilience
A consumer goods company used a low-code platform to develop a supply planning tool that incorporated real-time data from suppliers and production units. This improved supply chain resilience and reduced lead times by 20%.
5. Production Scheduling
Enhancing Production Scheduling
Efficient production scheduling is vital for meeting deadlines and optimising resource utilisation. Low-code and no-code platforms enhance production scheduling by:
- Automating Scheduling: Implementing automated scheduling systems that consider production capacity, labour availability, and demand forecasts.
- Real-Time Adjustments: Allowing real-time adjustments to schedules based on changing conditions.
- Resource Optimisation: Using data analytics to optimise resource allocation and reduce downtime.
Case Study: Increasing Production Efficiency
A pharmaceutical company used a no-code platform to develop a production scheduling tool that automated the scheduling process. This led to a 15% increase in production efficiency and a 10% reduction in operational costs.
6. Supplier Management
Strengthening Supplier Management
Effective supplier management is crucial for ensuring a reliable supply chain. Low-code and no-code solutions strengthen supplier management by:
- Automating Supplier Onboarding: Streamlining the supplier onboarding process with automated workflows.
- Supplier Performance Tracking: Implementing systems to track and evaluate supplier performance in real-time.
- Collaboration Tools: Developing collaborative platforms that facilitate communication and information sharing with suppliers.
Case Study: Enhancing Supplier Relationships
A food and beverage company used a low-code platform to automate supplier onboarding and performance tracking. This improved supplier relationships and reduced onboarding time by 50%.
7. KPI Reporting
Optimising KPI Reporting
Effective KPI reporting is essential for monitoring supply chain performance and making data-driven decisions. Low-code and no-code platforms optimise KPI reporting by:
- Custom Dashboards: Developing custom dashboards that display real-time KPIs.
- Automated Reports: Creating automated reporting systems that generate and distribute reports to stakeholders.
- Data Integration**: Integrating data from various sources to provide a comprehensive view of supply chain performance.
Case Study: Improving Decision-Making
A healthcare organisation used a no-code platform to develop custom KPI dashboards that integrated data from multiple sources. This enhanced decision-making and led to a 20% improvement in operational efficiency.
How Trace Consultants Can Help
Navigating the transition to low-code and no-code technology solutions can be challenging. Trace Consultants, a leading supply chain consulting firm, offers comprehensive support to help CIOs and CSCOs leverage these technologies effectively.
Strategic Advisory Services
Trace Consultants provides strategic advisory services to help CIOs and CSCOs develop and implement low-code and no-code solutions tailored to their specific needs. Their experts assess your current systems and processes, identify areas for improvement, and develop a roadmap for successful implementation.
Custom Application Development
With extensive experience in low-code and no-code platforms, Trace Consultants assists businesses in developing custom applications that address their unique supply chain challenges. Their team works closely with your organisation to create and deploy solutions that enhance efficiency and drive performance improvements.
Training and Support
Trace Consultants offers comprehensive training programs to ensure that your team can effectively use low-code and no-code platforms. Their training sessions cover platform functionalities, best practices, and troubleshooting, empowering your employees to develop and manage applications independently.
Continuous Improvement
Trace Consultants fosters a culture of continuous improvement by providing ongoing monitoring and support. They help businesses track performance metrics, gather user feedback, and implement enhancements to maintain optimal efficiency and effectiveness.
Case Studies and Success Stories
Trace Consultants has a proven track record of helping businesses achieve significant improvements through low-code and no-code solutions. Their success stories demonstrate the tangible benefits of these technologies, including increased efficiency, cost savings, and improved supply chain resilience.
Low-code and no-code technology solutions offer transformative potential for supply chain management. By enabling rapid development and deployment of custom applications, these platforms drive improvements across demand planning, inventory management, ordering, supply planning, production scheduling, supplier management, and KPI reporting.
Trace Consultants, with their expertise in supply chain management and technology solutions, provides valuable support to CIOs and CSCOs looking to leverage low-code and no-code platforms. By partnering with Trace Consultants, organisations can navigate the complexities of these technologies, achieve operational excellence, and maintain a competitive edge in the ever-evolving supply chain landscape.
Ready to turn insight into action?
We help organisations transform ideas into measurable results with strategies that work in the real world. Let’s talk about how we can solve your most complex supply chain challenges.