Ready to turn insight into action?
We help organisations transform ideas into measurable results with strategies that work in the real world. Let’s talk about how we can solve your most complex supply chain challenges.
Supply Chain Sustainability Reporting Series by Emma Woodberry
Part 1 - Sustainability Reporting
New Sustainability Reporting requirements are being introduced for Australian businesses and organisations
In June 2023, the ISSB released the inaugural global sustainability standards, which were an exercise in global baselining and alignment – in other words, getting everyone singing from the same song sheet when it comes to sustainability reporting. In March this year, a Treasury Bill was introduced into parliament which outlines the reporting obligations for Australian organisations, with commencement dates from 1 January 2025 – which is expected to be passed sometime this year. Organisations are encouraged to start preparing for what this means for their reporting requirements.
The reporting requirements will cover governance, strategy and risk management processes and controls in place for identifying and mitigating material sustainability related risks, including performance against sustainability metrics. These reporting obligations will have significant impacts on supply chain operations, as it will drive greater transparency, accountability and sustainability across entire value chains both locally and globally. Supply Chain leaders and managers may be called upon to report on or start measuring metrics against specific sustainability or climate related targets. Additional reporting requirements will be linked with existing financial reporting obligations at year end, so organisations will need to provide sustainability inputs to financial statements.
Reporting will need to address opportunities and risks as they relate to sustainability, for example, how climate change related disruption could impact an organisation’s ability to meet customer needs.

Reporting requirements will cover two key areas: Emissions and Climate related risk
Understand your Emissions
Measuring Scope 1 and 2 carbon emissions can be simple – mapping out your supply chain and determining the carbon footprint of your owned and controlled operations. Scope 3 is where the complexity begins – upstream activities can include the carbon footprint of all purchased goods and services, employee travel and waste generation for example, and downstream activities includes how sold products are used and disposed of. Do you know what happens to your products once they are in the customer’s hands?
Supply chain mapping is useful to understand where your value chain starts and ends, from processing of raw materials through to disposal of goods produced in your supply chain. This introduces the first layer of visibility of the extent of your Scope 3 emissions. From here it is important to understand what your suppliers and customers are doing to measure, manage and reduce their emissions, and how you are measuring, managing and mitigating your own emissions.
Risk and Resilience in your Supply Chain
Supply chain mapping provides a good overview of where emissions are generated across your value chain and will also provide a baseline for assessing climate change disruption risk. Conducting a risk and resilience assessment across your supply chain will identify areas of weakness or risk due to climate change related disruption. Areas such as critical infrastructure or vulnerability to disruption will be explored and assessed, identifying risk mitigating actions that need to be taken.
Moving Forward
Baselining your Scope 1, 2 and 3 emissions is the minimum, setting targets and management plans is the next step. This will involve operational initiatives that encourage efficiency within the organisation, as well as working with suppliers to increase transparency and visibility of upstream operations. Best practice then involves setting Science Based Targets (SBTs) that are ambitious and reporting progress against these targets.
Proactive risk mitigation steps for your supply chain extends to core supply chain efficiency activities such as network optimisation, supplier relationship management and lean inventory practices. Understanding your emissions and building a resilient supply chain will drive sustainable practice.
Where we can help
At Trace, we have tried and tested frameworks that support emissions baselining and measurement, as well as risk and resilience assessment.
Carbon Emissions Measurement
We can support you in understanding your emissions, identifying opportunities to reduce your footprint and improve your overall sustainability through the following high level 4-step approach:
1. Map your supply chain including your nodes, upstream supply chains, and downstream product lifecycles
2. Measure emissions using Greenhouse Gas (GHG) Protocol data (Scope 1, 2 and 3)
3. Set targets that are ambitious, measurable and supportive of strategic goals
4. Define and implement a set of initiatives that will support efficiency and emissions reduction activities
Our risk and resilience framework
Our Supply Chain Risk & Resilience Assessment Model aligns with the framework adopted by the Federal Office of Supply Chain Resilience and the Australian Productivity Commission, which are used to assess supply chain risks to critical products and services. Our model covers three stages:
1. Inputs Stage: identifies the qualitative and quantitative inputs to a resilience assessment including supply chain mapping, disruption scenarios, stakeholder engagement and existing plans and policies
2. Assessment Stage: measures the level of resilience, residual risks and sustainability impact through understanding the criticality and vulnerability of the supply chain
3. Actions Stage: identifies the key actions required to update and implement plans and policies that will secure future resilience and mitigate risks identified in Stage2
Understanding vulnerability to climate change disruption, and the actions being taken to overcome this vulnerability will be key requirements for future reporting regulations.
Get in touch today to see how we can help your supply chain sustainability journey.
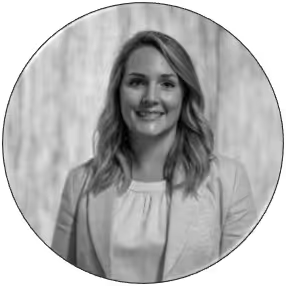
Emma Woodberry
Senior Manager
Ready to turn insight into action?
We help organisations transform ideas into measurable results with strategies that work in the real world. Let’s talk about how we can solve your most complex supply chain challenges.