Ready to turn insight into action?
We help organisations transform ideas into measurable results with strategies that work in the real world. Let’s talk about how we can solve your most complex supply chain challenges.
The Quick Service Restaurant (QSR) industry in Australia and New Zealand (ANZ) is poised for a transformative year in 2025. With margins under pressure and competition heating up, CEOs, CFOs, and CIOs face a dual challenge: how to enable growth while aggressively driving cost out of their supply chains and procurement operations. At Trace Consultants, we believe this is not just a balancing act—it’s an opportunity to unlock new levels of profitability and market leadership.
In this article, we’ll explore the trends shaping QSR supply chain and procurement projects in 2025, highlight strategies to fuel expansion and reduce costs, and show how Trace Consultants can partner with ANZ QSR leaders to deliver tangible results. Whether you’re a CEO eyeing market share, a CFO hunting for savings, or a CIO leveraging tech for efficiency, this guide will equip you to thrive in the year ahead.
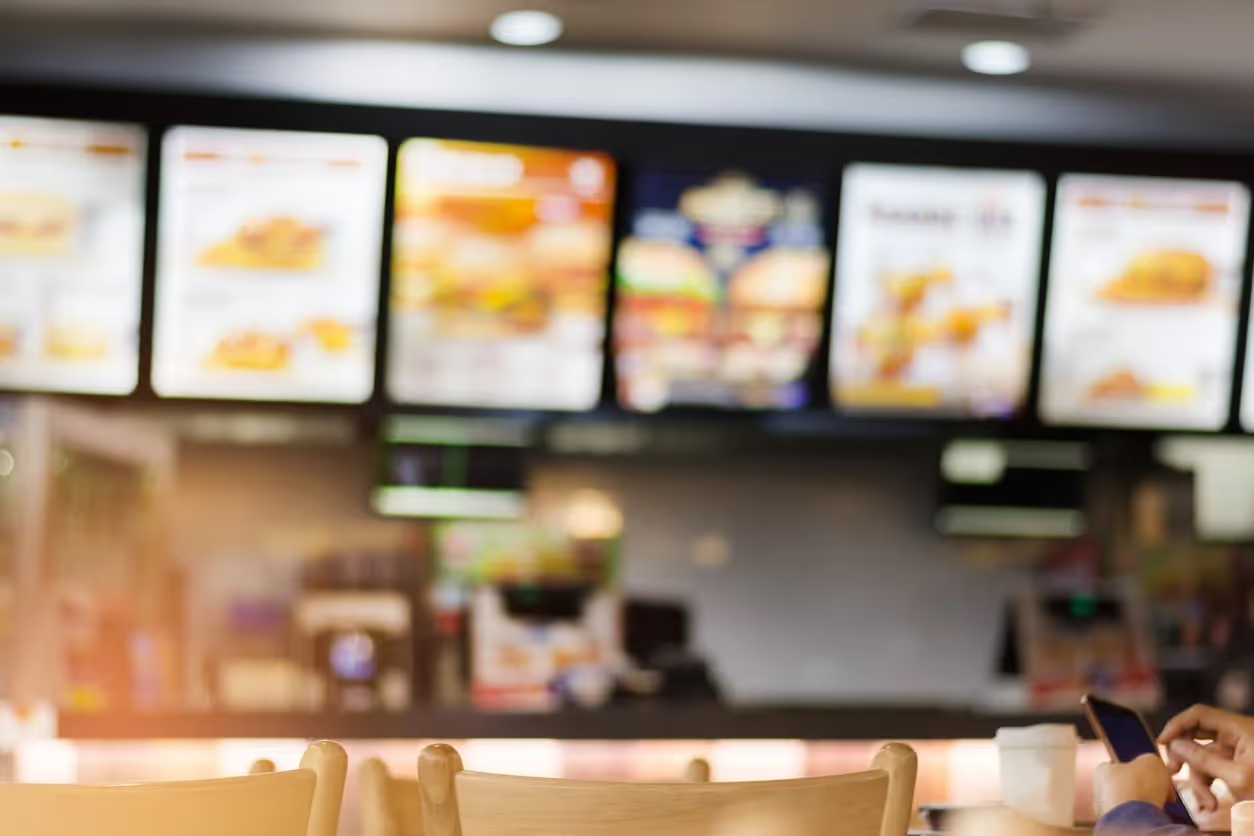
Why 2025 Is a Make-or-Break Year for QSR Growth and Cost Efficiency
The QSR sector—home to fast-food chains, takeaway joints, and coffee shops—thrives on delivering value at speed. In ANZ, brands like Hungry Jack’s, Subway, and Coffee Club have mastered this game, but 2025 brings fresh stakes. Inflation is pushing up costs for ingredients, labour, and logistics, while customers demand lower prices and faster service. At the same time, growth opportunities abound as urban populations swell and digital ordering surges.
For CEOs, this is a chance to capture new markets and boost revenue. For CFOs, it’s about slashing wasteful spend to protect the bottom line. And for CIOs, it’s an invitation to harness technology to make every process leaner and smarter. The key? A supply chain and procurement strategy that drives cost out while enabling scalable growth. Let’s dive into how ANZ QSRs can make it happen in 2025.
Key Trends Driving Growth and Cost Savings in QSR Supply Chains
Here are the five major trends shaping QSR supply chain and procurement projects in 2025—and how they can help you grow smarter and spend less.
1. Lean Procurement for Cost Reduction
Rising costs are the enemy of profitability, and procurement is ground zero for fighting back. In 2025, ANZ QSRs are rethinking how they source everything from beef patties to paper cups, focusing on leaner processes that eliminate waste and secure better deals.
For CFOs, this means renegotiating supplier contracts and consolidating purchasing power to drive down unit costs. CEOs can align these savings with growth plans—like funding new store openings—while CIOs enable it all with e-procurement platforms that automate and optimise buying.
How Trace Consultants Can Help:
At Trace Consultants, we’re experts at stripping cost out of procurement without compromising quality. We’ll analyse your spend data, identify overpriced inputs, and negotiate hard with suppliers to lock in savings. For CFOs, we deliver detailed ROI forecasts; for CIOs, we integrate tools like Coupa or SAP Ariba to streamline the process. Our goal? Help your QSR bank the savings you need to fuel growth.
2. AI-Powered Efficiency for Scalable Operations
Artificial Intelligence (AI) is a game-changer for QSRs in 2025, offering a one-two punch of cost reduction and growth enablement. Predictive analytics can forecast demand with pinpoint accuracy—say, how many pizzas you’ll sell on a Friday night—reducing overstock and waste. Automation can handle repetitive tasks like order processing, freeing up resources for expansion.
CFOs will see the impact in lower inventory costs and reduced labour spend. CEOs can use these efficiencies to scale operations into new regions, while CIOs lead the charge by integrating AI into supply chain systems.
How Trace Consultants Can Help:
Trace Consultants brings hands-on experience in deploying AI for ANZ QSRs. We’ll assess your tech needs, recommend solutions like AI-driven demand planning tools, and oversee a seamless rollout. Working with your CIO, we’ll ensure your systems deliver real-time insights that cut costs and support growth—whether you’re opening five new stores or fifty.
3. Local Supply Chains for Growth and Resilience
Global supply chains are costly and fragile, and in 2025, ANZ QSRs are going local to save money and grow faster. Sourcing from nearby suppliers cuts transport costs, speeds up delivery, and reduces exposure to international disruptions. It also unlocks growth by tapping into the “buy local” trend that resonates with ANZ customers.
CEOs can leverage this for brand expansion—think new outlets in regional towns with local supply support. CFOs will appreciate the lower logistics bills, and CIOs can build data platforms to manage these tighter, more responsive networks.
How Trace Consultants Can Help:
We specialise in redesigning supply chains for cost efficiency and scalability. Trace Consultants will map your supplier ecosystem, shift you to cost-effective local options, and model scenarios to balance savings with growth potential. Your CEO gets a roadmap to new markets, your CFO gets a leaner cost base, and your CIO gets a system that’s ready to scale.
4. Digital Transformation for Revenue and Savings
The digital boom—online orders, delivery apps, and loyalty programs—is driving QSR growth in 2025, but it’s also a goldmine for cost reduction. By digitising supply chain and procurement processes, QSRs can eliminate manual inefficiencies, reduce errors, and optimise resource use.
For CEOs, digital tools open doors to new revenue streams, like ghost kitchens or subscription models. CFOs can slash operational costs with automated workflows, and CIOs are the linchpin, ensuring these systems integrate smoothly across the business.
How Trace Consultants Can Help:
Trace Consultants has a track record of digitising ANZ QSR operations. We’ll pinpoint where manual processes are costing you, implement solutions like cloud-based ERP systems, and tie it all together for your CIO. The result? A digital backbone that drives revenue growth and cuts operational fat—giving your QSR the best of both worlds.
5. Workforce Optimisation to Support Expansion
Labour costs are a huge chunk of QSR budgets, and shortages in ANZ are pushing wages higher in 2025. Smart leaders are using automation—like robotic fry stations—and predictive workforce planning to do more with less. This frees up capital for growth while keeping costs in check.
CEOs can redirect labour savings into hiring for new locations. CFOs will love the leaner payroll, and CIOs can deploy tech like workforce management software to make it happen.
How Trace Consultants Can Help:
We’ve helped ANZ businesses optimise their workforce for growth and efficiency. Trace Consultants will assess your staffing model, introduce automation where it counts, and build predictive tools to match labour to demand. Your CIO gets a tech rollout that works, your CFO gets cost savings, and your CEO gets a team ready to scale.
Challenges to Growth and Cost Reduction in 2025
While the potential is massive, 2025 won’t be a cakewalk. Here are the hurdles ANZ QSRs need to overcome:
- Cost Pressures: Inflation and supply shortages could erode savings if not managed proactively.
- Tech Investment Risks: Big bets on AI or digital tools need to pay off quickly to justify the spend.
- Customer Retention: Growth depends on keeping price-sensitive diners happy amid rising costs.
- Execution Complexity: Scaling while cutting costs requires flawless coordination across teams.
These challenges are real, but they’re not roadblocks—they’re opportunities for QSRs with the right strategy and partner.
Opportunities for QSR CEOs, CFOs, and CIOs in 2025
In 2025, ANZ QSR leaders can turn trends into triumphs. Here’s how each role can drive growth and cost efficiency:
- CEOs: Expand boldly. Use lean supply chains and digital tools to enter new markets without bloating costs.
- CFOs: Hunt for savings. Slash procurement and operational expenses to fund growth without borrowing.
- CIOs: Build the future. Deploy tech that cuts waste and scales effortlessly as your QSR grows.
Together, you can create a QSR that’s leaner, stronger, and ready to dominate the ANZ market.
How Trace Consultants Can Help QSRs Grow and Save in 2025
At Trace Consultants, we’re not here to sell you a vision—we’re here to make it happen. With deep expertise in ANZ’s QSR and FMCG sectors, we deliver supply chain and procurement solutions that enable growth and drive cost out. Here’s how we can help:
- Cost-Out Procurement Strategies:
We’ll dissect your spend, negotiate better deals, and streamline purchasing to save you millions. Your CFO gets a tighter budget; your CEO gets cash for expansion. - AI and Digital Enablement:
From demand forecasting to automated workflows, we’ll implement tech that cuts costs and scales with your growth. Your CIO gets a partner who speaks their language. - Local Supply Chain Optimisation:
We’ll shift you to cost-efficient local suppliers, reducing logistics spend and supporting new store rollouts. Your CEO and CFO will see the impact fast. - S&OP for Growth and Efficiency:
Our Sales & Operations Planning frameworks align supply with demand, minimising waste and maximising revenue potential. It’s a win-win for all C-suite roles. - Workforce and Process Lean-Up:
We’ll automate where it makes sense and optimise labour planning, freeing up funds for your next big move. Your CIO and CFO will thank us.
Our approach is practical, data-driven, and collaborative. We work shoulder-to-shoulder with your team to deliver results—not just recommendations. With Trace Consultants, you’re not just surviving 2025—you’re setting the pace for the industry.
The Road Ahead: Growth Without the Bloat
In 2025, ANZ QSRs don’t have to choose between growth and cost efficiency—they can have both. By leaning into smart procurement, local supply chains, and cutting-edge tech, you can expand your footprint while keeping costs razor-sharp. For CEOs, it’s about leading with ambition. For CFOs, it’s about protecting profitability. For CIOs, it’s about building systems that deliver.
Ready to make 2025 your year? Contact Trace Consultants today. Let’s drive cost out and growth up—together.
Ready to turn insight into action?
We help organisations transform ideas into measurable results with strategies that work in the real world. Let’s talk about how we can solve your most complex supply chain challenges.