Ready to turn insight into action?
We help organisations transform ideas into measurable results with strategies that work in the real world. Let’s talk about how we can solve your most complex supply chain challenges.
As the global focus on sustainability intensifies, businesses worldwide are being held to increasingly stringent environmental standards. In Australia, new regulations around Scope 3 emissions are set to reshape how companies report and manage their carbon footprints. For CEOs and CFOs, understanding these changes is crucial not only for compliance but also for leveraging opportunities for strategic advantage. This article explores what to expect from the new Scope 3 regulations, how to prepare your organisation, and how Trace Consultants can support you in this journey.
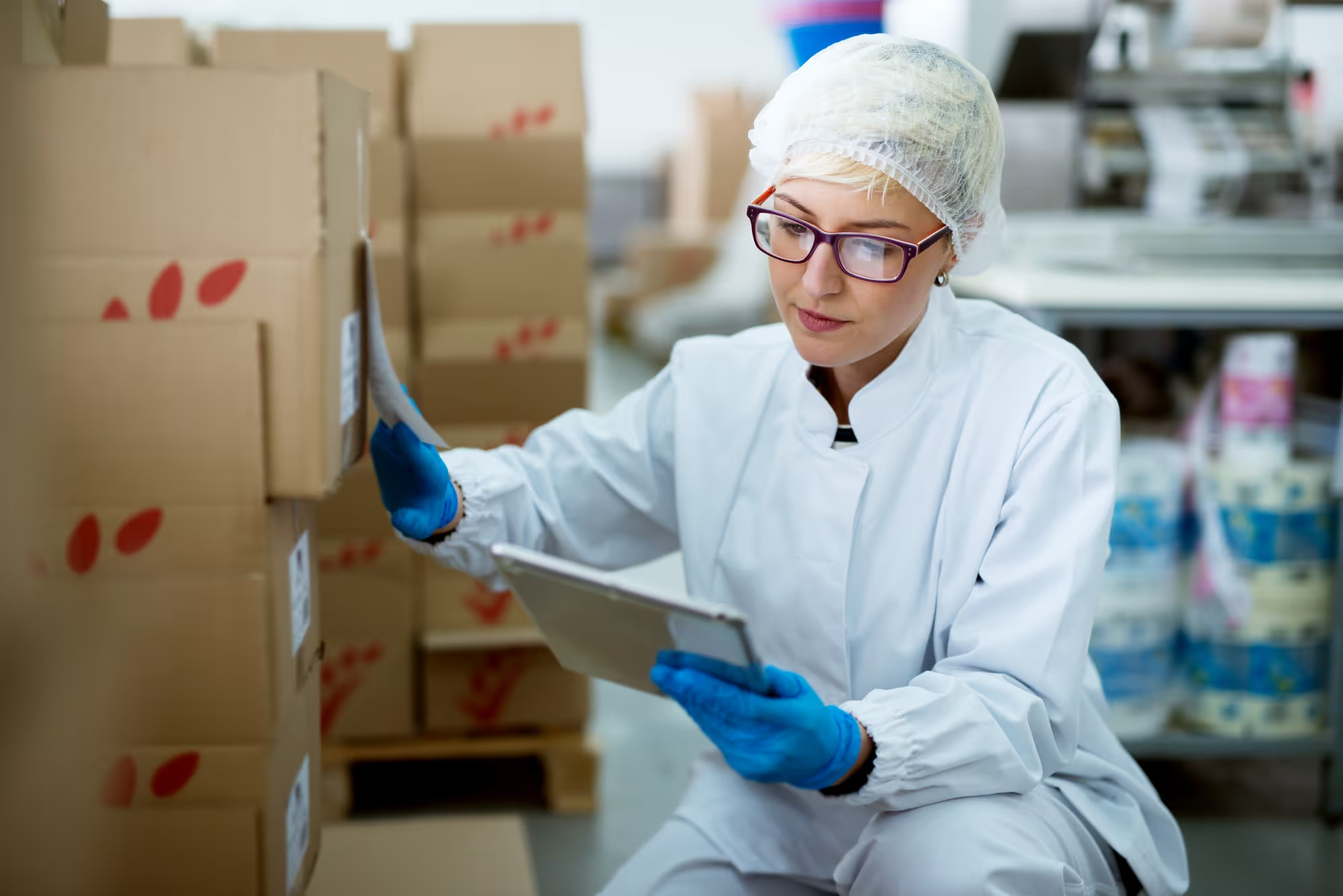
What are Scope 3 Emissions?
Scope 3 emissions encompass all indirect emissions that occur in a company's value chain. Unlike Scope 1 and Scope 2 emissions, which cover direct emissions from owned or controlled sources and indirect emissions from the generation of purchased electricity, Scope 3 emissions span a wide range of activities. These include emissions from purchased goods and services, business travel, employee commuting, waste disposal, and more.
The New Scope 3 Regulations in Australia
The Australian government is introducing new regulations that require businesses to comprehensively report their Scope 3 emissions. These changes are part of a broader effort to meet national and international climate targets and enhance transparency in corporate sustainability practices. Key aspects of the new regulations include:
- Mandatory Reporting: Companies will be required to report Scope 3 emissions in their annual sustainability reports.
- Increased Transparency: Enhanced disclosure requirements will necessitate detailed reporting on the methodologies used for calculating emissions.
- Third-Party Verification: Independent verification of reported emissions data to ensure accuracy and credibility.
- Target Setting: Businesses will need to set and disclose Scope 3 emissions reduction targets aligned with national and international climate goals.
Implications for Businesses
The new Scope 3 regulations present both challenges and opportunities for businesses. Compliance will require significant effort, particularly in gathering and verifying data across the entire value chain. However, these regulations also offer a chance to drive operational efficiencies, enhance brand reputation, and strengthen stakeholder relationships.
- Data Collection and Management: Accurate reporting of Scope 3 emissions requires robust data collection processes. Businesses must engage with suppliers, customers, and other stakeholders to gather necessary information.
- Risk Management: Understanding and managing Scope 3 emissions can help identify risks in the supply chain, such as reliance on carbon-intensive suppliers.
- Competitive Advantage: Companies that proactively address Scope 3 emissions can differentiate themselves in the market, attracting environmentally conscious consumers and investors.
- Innovation and Efficiency: The drive to reduce Scope 3 emissions can spur innovation, leading to more sustainable products and services.
Preparing for the New Regulations
Preparation is key to navigating the new Scope 3 regulations successfully. Here are some steps CEOs and CFOs can take to ensure their organisations are ready:
- Understand the Requirements: Familiarise yourself with the specific requirements of the new regulations. This includes understanding the reporting standards, verification processes, and target-setting guidelines.
- Assess Your Current State: Conduct a comprehensive assessment of your current Scope 3 emissions. Identify key sources of emissions and evaluate your existing data collection and reporting processes.
- Engage Stakeholders: Collaborate with suppliers, customers, and other stakeholders to gather accurate emissions data. Establish clear communication channels and set expectations for data sharing and reporting.
- Invest in Technology: Implement advanced data management systems to streamline the collection, analysis, and reporting of emissions data. This can include software solutions that automate data gathering and provide real-time insights.
- Set Ambitious Targets: Develop and disclose ambitious but achievable Scope 3 emissions reduction targets. Align these targets with national and international climate goals to demonstrate your commitment to sustainability.
- Monitor and Report Progress: Regularly monitor your progress towards emissions reduction targets. Publish detailed sustainability reports that highlight your achievements and areas for improvement.
- Seek External Expertise: Engage with consultants and experts who can provide guidance on best practices for Scope 3 emissions management and reporting.
Leveraging AI and Supply Chain N-Tier Analysis
Artificial Intelligence (AI) and supply chain n-tier analysis are powerful tools that can significantly enhance your organisation’s ability to comply with the new Scope 3 regulations and achieve emissions reduction targets.
How AI Can Help
- Data Processing and Analysis: AI can process vast amounts of data quickly and accurately, identifying patterns and insights that would be difficult or impossible for humans to detect. This is particularly useful for analysing complex supply chain data and calculating Scope 3 emissions.
- Predictive Analytics: AI can predict future emissions based on current data, helping businesses to forecast their environmental impact and make proactive changes.
- Optimisation: AI algorithms can optimise supply chain operations to reduce emissions. This includes route optimisation for logistics, energy-efficient production scheduling, and inventory management to minimise waste.
- Real-Time Monitoring: AI-powered tools can provide real-time monitoring of emissions, allowing businesses to track their progress towards reduction targets and make adjustments as needed.
The Role of Supply Chain N-Tier Analysis
- Comprehensive Emissions Mapping: N-tier analysis enables businesses to map emissions across multiple tiers of their supply chain, providing a complete picture of their Scope 3 emissions.
- Supplier Engagement: By understanding the emissions contributions of each supplier, businesses can engage more effectively with their supply chain partners to implement sustainability initiatives.
- Risk Identification: N-tier analysis helps identify risks related to supplier dependencies and carbon-intensive activities, allowing businesses to develop mitigation strategies.
- Transparency and Accountability: Detailed analysis across all supply chain tiers enhances transparency and accountability, meeting regulatory requirements and building trust with stakeholders.
How Trace Consultants Can Help
Navigating the complexities of the new Scope 3 regulations can be daunting, but you don’t have to do it alone. Trace Consultants offers comprehensive support to help businesses comply with these regulations and leverage opportunities for strategic advantage.
- Expert Guidance: Our team of experts stays abreast of the latest regulatory developments and can provide detailed guidance on compliance requirements.
- Data Collection and Analysis: We assist in setting up robust data collection and management systems, ensuring accurate and efficient reporting of Scope 3 emissions.
- AI and N-Tier Analysis Integration: We help you integrate AI and supply chain n-tier analysis into your sustainability strategy, enhancing data accuracy, predictive capabilities, and overall emissions management.
- Stakeholder Engagement: We facilitate collaboration with your suppliers and other stakeholders, helping to establish clear communication channels and data-sharing protocols.
- Target Setting and Reporting: We help you develop realistic and ambitious emissions reduction targets and support you in preparing detailed sustainability reports that meet regulatory standards.
- Risk Management: Our consultants work with you to identify and mitigate risks associated with Scope 3 emissions, enhancing your overall risk management strategy.
- Sustainability Strategy: Beyond compliance, we help you integrate sustainability into your core business strategy, driving innovation and competitive advantage.
The new Scope 3 regulations in Australia represent a significant shift in how businesses manage and report their carbon footprints. For CEOs and CFOs, understanding these changes and preparing accordingly is crucial. By taking proactive steps to comply with these regulations, businesses can not only avoid penalties but also unlock opportunities for innovation, efficiency, and competitive advantage.
AI and supply chain n-tier analysis are indispensable tools in this endeavour, offering advanced capabilities for data analysis, predictive insights, and operational optimisation. Trace Consultants is here to support you through this transition. With our expertise in sustainability and supply chain management, we can help you navigate the complexities of the new regulations and achieve your sustainability goals. Contact us today to learn more about how we can assist your organisation in this critical journey towards a more sustainable future.
----
As new Scope 3 regulations take effect in Australia, CEOs and CFOs must understand the implications for their businesses. This article outlines what these changes entail, how to prepare, and how Trace Consultants can assist in navigating this complex regulatory landscape.
Discover what the new Scope 3 regulations in Australia mean for your business, how to prepare, and how Trace Consultants can guide you through compliance and optimisation strategies.
Ready to turn insight into action?
We help organisations transform ideas into measurable results with strategies that work in the real world. Let’s talk about how we can solve your most complex supply chain challenges.