Ready to turn insight into action?
We help organisations transform ideas into measurable results with strategies that work in the real world. Let’s talk about how we can solve your most complex supply chain challenges.
Australia's defence capability hinges not just on the acquisition of cutting-edge technology and heavy assets but, more crucially, on the robustness and resilience of its supply chains. In the theatre of global defence, it's an often-repeated adage that while acquisition may win battles, sustainment wins wars. This blog delves into the intricate world of Australia's defence supply chains, focusing on heavy asset management and Maintenance, Repair, and Overhaul (MRO) logistics, and explores the critical attributes that can forge a competitive advantage in times of uncertainty.
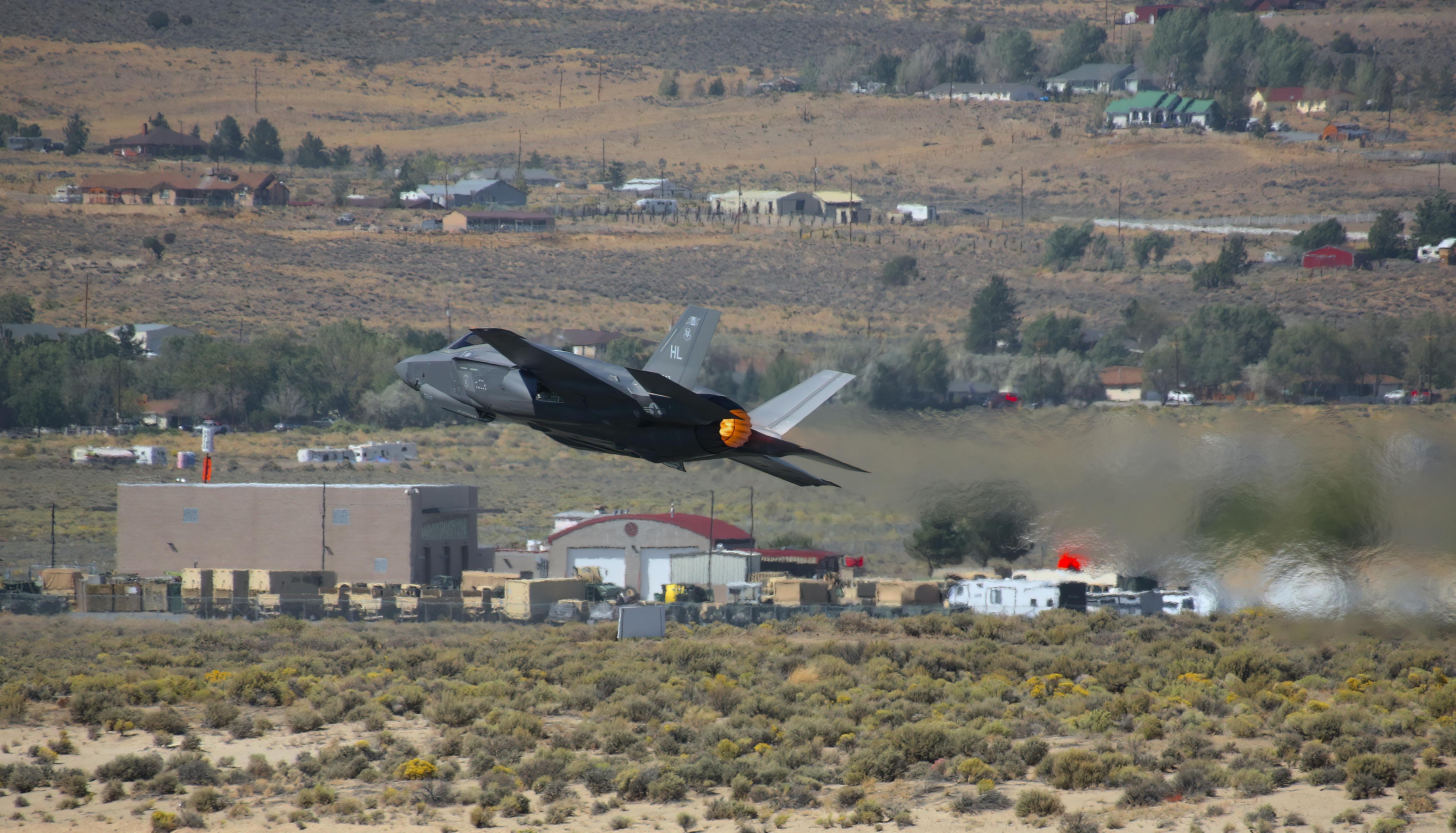
Understanding the Strategic Importance of Defence Sustainment
Sustainment in the defence sector refers to the comprehensive support and maintenance activities required to keep military assets operational over their life cycle. This includes the procurement of spare parts, repairs, overhauls, and upgrades necessary to maintain readiness and extend the operational life of military equipment. For Australia, a country with vast territories and strategic interests in the Indo-Pacific region, the efficiency and reliability of defence sustainment activities are paramount.
Heavy Asset and MRO Supply Chains
Heavy assets in defence include armoured vehicles, naval ships, aircraft, and complex weapon systems, all requiring meticulous maintenance and timely support. The Maintenance, Repair, and Overhaul (MRO) of these assets is a complex logistical endeavour, involving a network of suppliers, technicians, and logistics platforms. The Australian Defence Force (ADF) relies on an intricate MRO supply chain to ensure that these assets are mission-ready at all times.
Key Attributes for Competitive Advantage
In the face of geopolitical tensions and the increasing pace of technological change, the attributes that define a competitive advantage in defence supply chains are resilience, agility, and innovation. Here's how these attributes translate into operational excellence:
- Resilience: The ability to withstand disruptions, such as natural disasters or geopolitical conflicts, is crucial. This involves diversifying supply sources, maintaining strategic stockpiles, and developing contingency plans.
- Agility: Quick response to changing operational demands is vital. This means having flexible logistics and adaptable supply chain networks that can pivot as required.
- Innovation: Leveraging technology to streamline supply chain processes, from predictive maintenance to digital twins, can dramatically enhance efficiency and readiness.
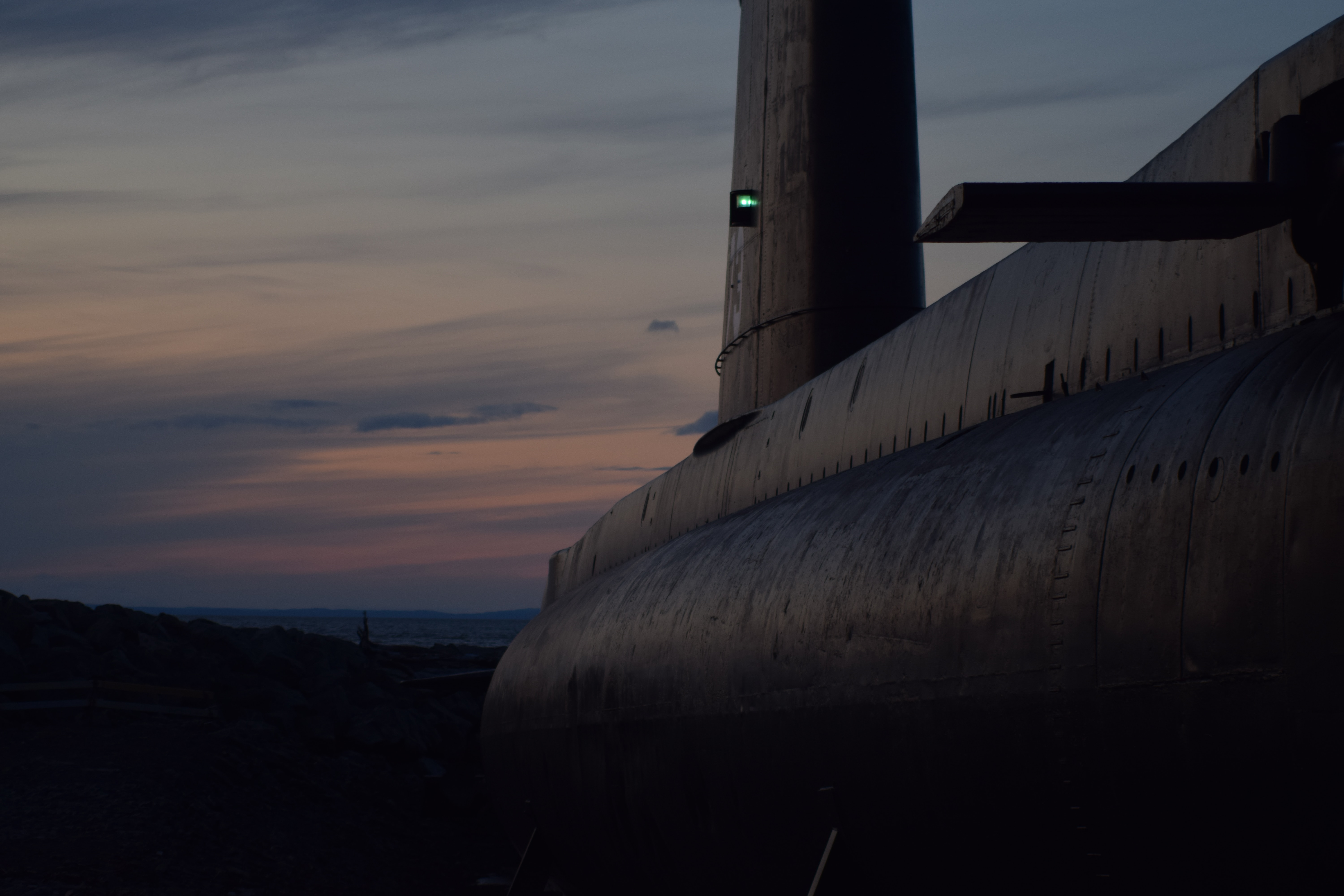
Demand Planning and Service
Effective demand planning and service delivery are at the heart of defence sustainment. This involves accurately forecasting the need for spare parts and maintenance services and ensuring that these are delivered where and when needed. Advanced analytics and AI play a significant role in enhancing demand forecasting, allowing for more precise planning and inventory management.
Constraint-based Optimisation and Supply Replenishment
Constraint-based optimisation involves identifying and managing the bottlenecks that limit the efficiency of supply chains. In the context of defence, this could mean prioritising the repair of critical assets or optimising the distribution network to ensure timely replenishment of supplies. Supply and replenishment planning ensures that all elements of the defence force are adequately stocked with the necessary parts and materials, minimising downtime and ensuring operational readiness.
Scenario Modelling and Network Optimisations
Scenario modelling involves using simulations to understand the impact of different operational scenarios on supply chain performance. This can help defence planners prepare for a range of contingencies, from sudden spikes in demand to disruptions in the supply network. Network optimisation tools can then be used to design a logistics network that balances efficiency with resilience, ensuring that resources are optimally allocated across the supply chain.
Logistics Execution
The final piece of the puzzle is logistics execution – the actual transportation, warehousing, and delivery of supplies. In Australia, with its unique geographical challenges, this often involves a mix of land, air, and sea logistics solutions. Advanced tracking and management systems ensure that assets are delivered efficiently and safely, with real-time visibility into the status of shipments.
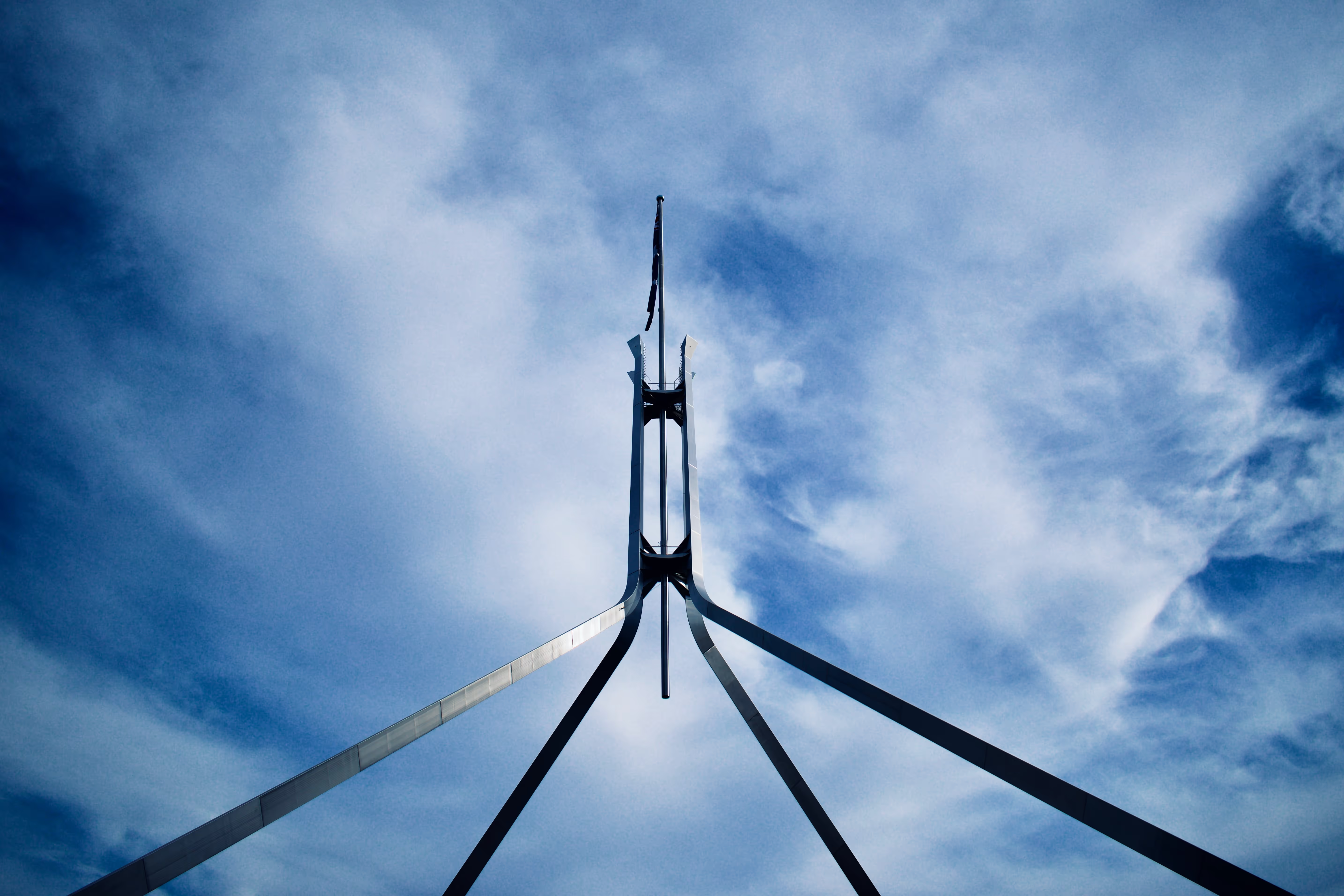
For Australia, building a defence capability that can withstand the challenges of the 21st century requires more than just investing in the latest technology. It demands a holistic approach to sustainment, one that prioritises resilience, agility, and innovation across all aspects of the defence supply chain. From demand planning and service delivery to logistics execution, each component must be optimised to ensure that the ADF remains ready and capable of defending the nation's interests.
In uncertain times, the strength of Australia's defence does not lie solely in its fleet of aircraft or its arsenal of missiles but in the reliability and efficiency of its supply chains. As the global security landscape evolves, sustaining this capability will be the key to ensuring that Australia can not only win battles but sustain a winning strategy in the long term.
The recent AUKUS submarine deal represents a monumental shift in Australia's defence landscape, necessitating a significant transformation in the nation's sustainment, heavy asset, and MRO (Maintenance, Repair, and Overhaul) supply chain capabilities. This landmark agreement, which sees Australia entering into a strategic partnership with the United States and the United Kingdom to acquire nuclear-powered submarines, underscores the increasing complexity and technological sophistication of modern military assets. The integration of these advanced submarines into Australia's defence arsenal will require an unprecedented level of support in terms of maintenance, technical expertise, and supply chain logistics.
The step-change demanded by the AUKUS deal goes beyond the mere acquisition of new equipment; it encompasses the development of a robust infrastructure capable of supporting high-tech, nuclear-powered vessels over their operational lifecycle. This entails not just the physical maintenance of the submarines but also the management of a complex network of suppliers and the continuous updating of spare parts and materials. The deal highlights the need for Australia to enhance its MRO capabilities, ensuring that the nation can maintain operational readiness and technological superiority.
Moreover, the AUKUS submarine deal brings to the forefront the importance of international collaboration in supply chain management. As Australia navigates the intricacies of integrating these advanced submarines, working closely with its AUKUS partners will be crucial in developing a shared understanding of best practices in sustainment and logistics. This collaboration will likely spur innovations in supply chain management and operational logistics, setting new standards for the sustainment of high-value, technologically advanced defence assets.
In summary, the AUKUS submarine deal is not just a significant military acquisition for Australia; it is a catalyst for transforming the country's defence supply chains. It necessitates a comprehensive reevaluation of current sustainment practices and a concerted effort to elevate Australia's heavy asset and MRO supply chain capabilities to meet the demands of 21st-century warfare. This transformation will be instrumental in ensuring that Australia maintains its strategic edge in an increasingly complex and uncertain global security environment.
Ready to turn insight into action?
We help organisations transform ideas into measurable results with strategies that work in the real world. Let’s talk about how we can solve your most complex supply chain challenges.