Ready to turn insight into action?
We help organisations transform ideas into measurable results with strategies that work in the real world. Let’s talk about how we can solve your most complex supply chain challenges.
In today's dynamic business environment, the supply chain extends beyond a mere backend operation; it emerges as a pivotal competitive edge. However, sculpting a supply chain that marries efficiency with resilience demands a considered approach to organisational design. This task is not only about structuring the supply chain to satisfy present demands but also about forecasting and prepping for future hurdles and opportunities. Our exploration delves into the core facets of supply chain organisational design, such as operating model design, workforce strategy, the debate between insourcing and outsourcing, capability gap assessment, the crafting of job roles, and the enactment of the RACI framework. Furthermore, we underscore how the organisational context—be it a quest for growth necessitating scalability or a crunch for cost leading to a drive for efficiency and resilience—can significantly mould these design principles.
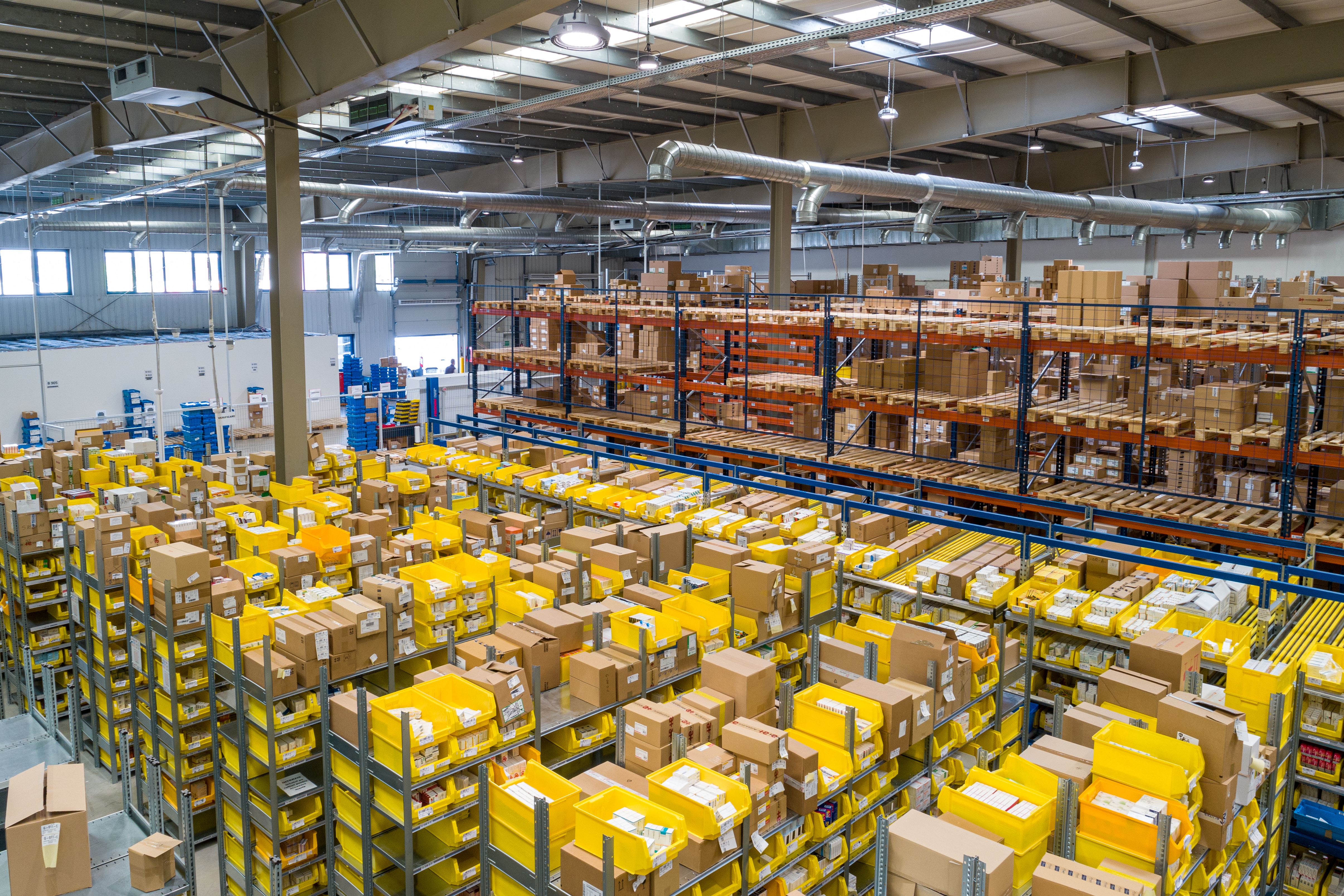
Operating Model Design: Warehouse, Transport, and Operations
An efficacious supply chain organisation is rooted in its operating model, which encompasses warehouse logistics, transportation, and overarching operations management. The blueprinting of this model necessitates an intimate grasp of the company's strategic pursuits. For instance, a business eyeing growth may lean towards scalability and adaptability in its warehouse operations, potentially opting for expansive facilities decked with cutting-edge automation tech. In contrast, a firm grappling with cost pressures might zero in on optimising existing assets, deploying lean inventory stratagems, and securing more cost-effective transportation agreements to pare down overhead.
Warehouse Operations
The linchpin of proficient warehouse operations lies in strategic layout planning, adept inventory management, and the seamless integration of technology. The deployment of automation, through robotics and AI-managed systems, can significantly uplift productivity and precision. Nonetheless, these tech investments must resonate with the company's long-term strategic vision and capacity planning.
Transportation and Logistics
The transportation strategy is equally paramount, entailing mode selection, route optimisation, and forging solid carrier alliances. Leveraging advanced analytics can illuminate the most economical transport modes and routes, yet this demands a workforce skilled in data interpretation and strategic decision-making.
Operations Management
Operations management acts as the glue binding everything together, with a spotlight on process efficiency, quality assurance, and the ethos of continuous improvement. The objective is to ensure the supply chain operates as a unified, nimble entity, ready to pivot in response to market flux.
Workforce Strategy & Composition
The cornerstone of any potent supply chain is its workforce, underpinned by a well-conceived blend of skills and roles tailored to operational objectives. This includes navigating the intricate balance between insourcing and outsourcing and the nuanced mix of full-time, part-time, casual, and contingent labour.
Insource vs. Outsource
The insource versus outsource conundrum is layered, shaped by cost considerations, the desire for control, expertise, and scalability. Insourcing can foster greater alignment with the company ethos and quality benchmarks but necessitates substantial investment in recruitment, training, and infrastructure. Outsourcing, meanwhile, offers adaptability and access to specialised skill sets, albeit with potential trade-offs in quality oversight and communication fluidity.
Labour Mix
Crucial to the workforce strategy is striking the right chord in the mix of full-time, part-time, casual, and contingent workers. This balance is pivotal for managing labour costs effectively while ensuring the workforce remains responsive and adaptable to changing demands. Full-time employees provide stability and in-depth knowledge of operations, while part-time and casual workers offer flexibility to scale labour in response to fluctuating workloads. Contingent labour, including freelancers and contractors, allows companies to tap into specialised skills on an as-needed basis, offering a blend of expertise without the commitment of full-time hires. This nuanced approach to workforce composition is integral to a resilient and efficient supply chain, ensuring the right skills are available at the right time and in the right proportion.
Team Capability Gap Assessment and Training Needs Assessment
Identifying and bridging capability gaps within the team is vital for perpetual advancement. This entails evaluating the existing workforce's skills and knowledge against the competencies required to realise strategic ambitions. Subsequently, a training needs assessment can spotlight specific development areas, fortifying the organisation's capacity to embrace new technologies, methodologies, and market shifts.
Job Roles and Description Design
The articulation of clear, comprehensive job roles and descriptions is pivotal for organisational lucidity and employee morale. This clarity is instrumental in a supply chain milieu, where cross-functional synergy is crucial for operational fluency.
RACI Framework Implementation
The RACI framework (Responsible, Accountable, Consulted, Informed) serves as an invaluable tool for demarcating roles and responsibilities within supply chain processes. Its implementation can streamline decision-making, mitigate overlaps and responsibility voids, and enhance inter-team and departmental communication.
The Influence of Organisational Context
The aforementioned design tenets are not universally applicable; they necessitate customisation to the unique backdrop of the organisation. Whether the goal is scaling for growth or honing efficiency, the strategic approach to supply chain organisational design must be in harmonious alignment with the company’s overarching objectives and situational demands.
Designing a robust supply chain organisation is a complex yet crucial endeavour. It mandates a strategic orientation towards operating model design, workforce strategy, and the nuanced balance between insourcing and outsourcing. Additionally, recognising the significance of team capability, precise role definition, and the RACI framework is essential for operational triumph. Nonetheless, the quintessence of supply chain organisational design lies in its congruence with the strategic imperatives and contextual nuances of the company. Through a comprehensive and strategic approach to supply chain organisational design, businesses can forge a supply chain that not only confronts today's challenges head-on but is also well-equipped for the opportunities and trials of tomorrow.
Ready to turn insight into action?
We help organisations transform ideas into measurable results with strategies that work in the real world. Let’s talk about how we can solve your most complex supply chain challenges.