Ready to turn insight into action?
We help organisations transform ideas into measurable results with strategies that work in the real world. Let’s talk about how we can solve your most complex supply chain challenges.
Why BOH Operations Matter in Hospital Development
Hospital master planning is a complex undertaking that shapes the functionality, safety, and efficiency of a healthcare facility for decades to come. While much attention is given to clinical spaces, patient experience, and aesthetics, one critical yet often overlooked aspect is back-of-house (BOH) operations.
BOH areas—loading docks, supply chain logistics, waste management, food service, linen handling, and sterile processing—are the lifeblood of hospital operations. Poor planning can lead to safety risks, inefficiencies, traffic congestion, compliance failures, and escalating costs to serve.
This is particularly critical in the Asia-Pacific (APAC) region, where rapid urbanisation, population growth, and ageing demographics are driving demand for efficient, scalable, and cost-effective healthcare facilities.
This article explores why BOH operations must be prioritised in hospital master planning to mitigate risks and optimise performance.
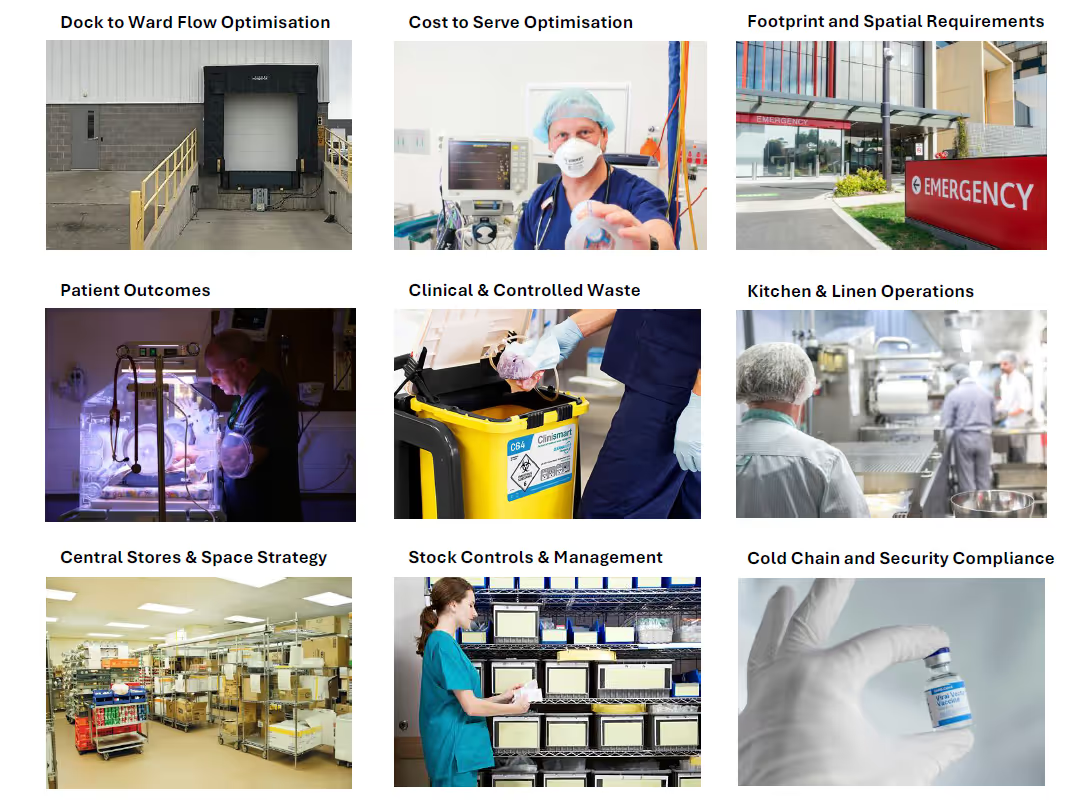
1. BOH Infrastructure & Traffic Management: Mitigating Safety & Congestion Risks
The Challenge: Overcrowded Loading Docks & BOH Corridors
Many hospitals in densely populated APAC cities face severe congestion in their BOH areas due to:
❌ High delivery volumes from multiple suppliers
❌ Poorly designed loading docks that create bottlenecks
❌ Limited space for goods movement
❌ Inadequate separation of hospital staff, suppliers, and patients
Without careful planning, these issues lead to:
⚠ Traffic congestion → Delayed deliveries & increased logistics costs
⚠ Worker & patient safety hazards → Risk of accidents in loading dock areas
⚠ Service inefficiencies → Staff spending more time managing deliveries instead of patient care
The Solution: Smart BOH Design & Traffic Flow Optimisation
Hospitals can proactively mitigate these risks through:
✔ Optimised loading dock layouts → Dedicated zones for deliveries, waste removal & linen services
✔ Vehicle scheduling & dock appointment systems → Reduces congestion & waiting times
✔ Separation of BOH & patient flow → Avoids cross-contamination & ensures HACCP compliance
✔ Use of Automated Guided Vehicles (AGVs) → Minimises manual handling & enhances safety
Strategic BOH master planning ensures that logistics and clinical operations are seamlessly integrated, reducing traffic risks, service disruptions, and operational costs.
2. Cost-to-Serve & Operational Efficiency: The Hidden ROI of BOH Planning
The Challenge: Uncontrolled Operating Costs Due to Poor BOH Design
If BOH operations are not considered early, hospitals face higher long-term costs from:
❌ Inefficient workflows → Increased manual labour & staff fatigue
❌ Excessive stockholding & poor inventory management → Inflated working capital costs
❌ Poor layout of central stores → Inefficient picking & replenishment
❌ High transport & distribution costs → Due to suboptimal supply chain networks
The Solution: Integrated BOH & Supply Chain Design
✔ Centralised inventory hubs & demand-driven replenishment → Reduces waste & storage costs
✔ Dock-to-ward optimisation strategies → Direct line replenishment minimises stock-outs
✔ Automated storage & retrieval systems (ASRS) → Improves accuracy & labour efficiency
✔ Demand forecasting & AI-driven inventory models → Reduces carrying costs while ensuring supply availability
When hospitals design BOH operations with a supply chain mindset, they unlock significant savings in labour, inventory, logistics, and utilities, making long-term operations more financially sustainable.
3. Food & Linen Services: HACCP & Compliance Considerations
The Challenge: Food Safety & Linen Handling Risks in Hospital BOH Areas
Hospital food & linen services present serious risks if BOH workflows are not carefully managed:
⚠ Cross-contamination risks → Poor segregation of clean & dirty zones
⚠ HACCP non-compliance → Leading to regulatory penalties & foodborne illness risks
⚠ Delivery bottlenecks → Late meal & linen replenishments impacting patient care
The Solution: BOH Design for Safe & Compliant Service Delivery
Hospitals must adopt purpose-built BOH spaces with:
✔ Separate entry & exit zones for food, linen, and waste flows
✔ Temperature-controlled food storage & distribution areas
✔ Barrier workflows & segregated waste handling for infection control
✔ Digital traceability & HACCP-compliant food monitoring systems
By designing BOH with compliance at the core, hospitals avoid safety risks, regulatory issues, and costly operational inefficiencies.
4. Waste Management & Sustainability: Future-Proofing BOH for Green Hospitals
The Challenge: Rising Waste Volumes & Sustainability Pressures
Hospitals generate enormous waste streams, including:
🗑 Clinical & biohazard waste → Requires strict disposal protocols
♻ Recyclable & general waste → Growing regulatory pressure for sustainability
🍽 Food & organic waste → Needs proper composting & disposal
Poor BOH waste handling leads to:
❌ Environmental & regulatory compliance risks
❌ Odour, hygiene & pest control challenges
❌ High disposal costs & inefficiencies
The Solution: Sustainable BOH Waste Management
✔ Automated waste chutes & pneumatic waste disposal → Reduces contamination risks
✔ Recycling & circular waste economy → Reduces landfill impact
✔ On-site food waste digesters & composting → Sustainable F&B operations
✔ Green building certifications → Aligns with APAC healthcare sustainability goals
Hospitals that integrate sustainable BOH waste systems achieve lower costs, better hygiene, and regulatory compliance while improving their environmental footprint.
BOH Master Planning—A Critical Success Factor for APAC Hospital Developments
As APAC’s healthcare infrastructure expands, hospital developments must prioritise BOH operations in the Master Planning phase to:
✅ Avoid congestion, traffic & safety risks → Through smart loading dock & logistics design
✅ Optimise cost-to-serve & service efficiency → By integrating BOH & supply chain strategies
✅ Ensure HACCP compliance & safe food/linen services → Through workflow segregation & monitoring
✅ Implement sustainable waste management → To align with green hospital standards
Neglecting BOH operations in master planning creates long-term operational challenges that are costly, inefficient, and difficult to fix post-construction.
Is your hospital project designing for BOH success? By engaging supply chain and healthcare logistics specialists early, APAC hospital developments can achieve safer, more efficient, and future-proof healthcare infrastructure.
Ready to turn insight into action?
We help organisations transform ideas into measurable results with strategies that work in the real world. Let’s talk about how we can solve your most complex supply chain challenges.