Ready to turn insight into action?
We help organisations transform ideas into measurable results with strategies that work in the real world. Let’s talk about how we can solve your most complex supply chain challenges.
In 2025, Maintenance, Repair, and Operations (MRO) supply chains are a critical concern for Government and Energy Provider companies in Australia and New Zealand (ANZ), especially in the coal-fired energy sector. High operational costs, driven by aging infrastructure and a reliance on unplanned, reactive maintenance, are straining budgets and threatening reliability. At Trace Consultants, we’re committed to helping ANZ energy providers and government bodies optimise their MRO supply chains to reduce costs, improve efficiency, and ensure sustainable energy delivery.
This article delves into the challenges of MRO supply chains in coal-fired energy, focusing on the impact of old assets and unplanned maintenance. We’ll explore strategies to address these issues, tailored for ANZ’s unique energy landscape, and highlight how Trace Consultants can support Government and Energy Providers in transforming their maintenance operations.
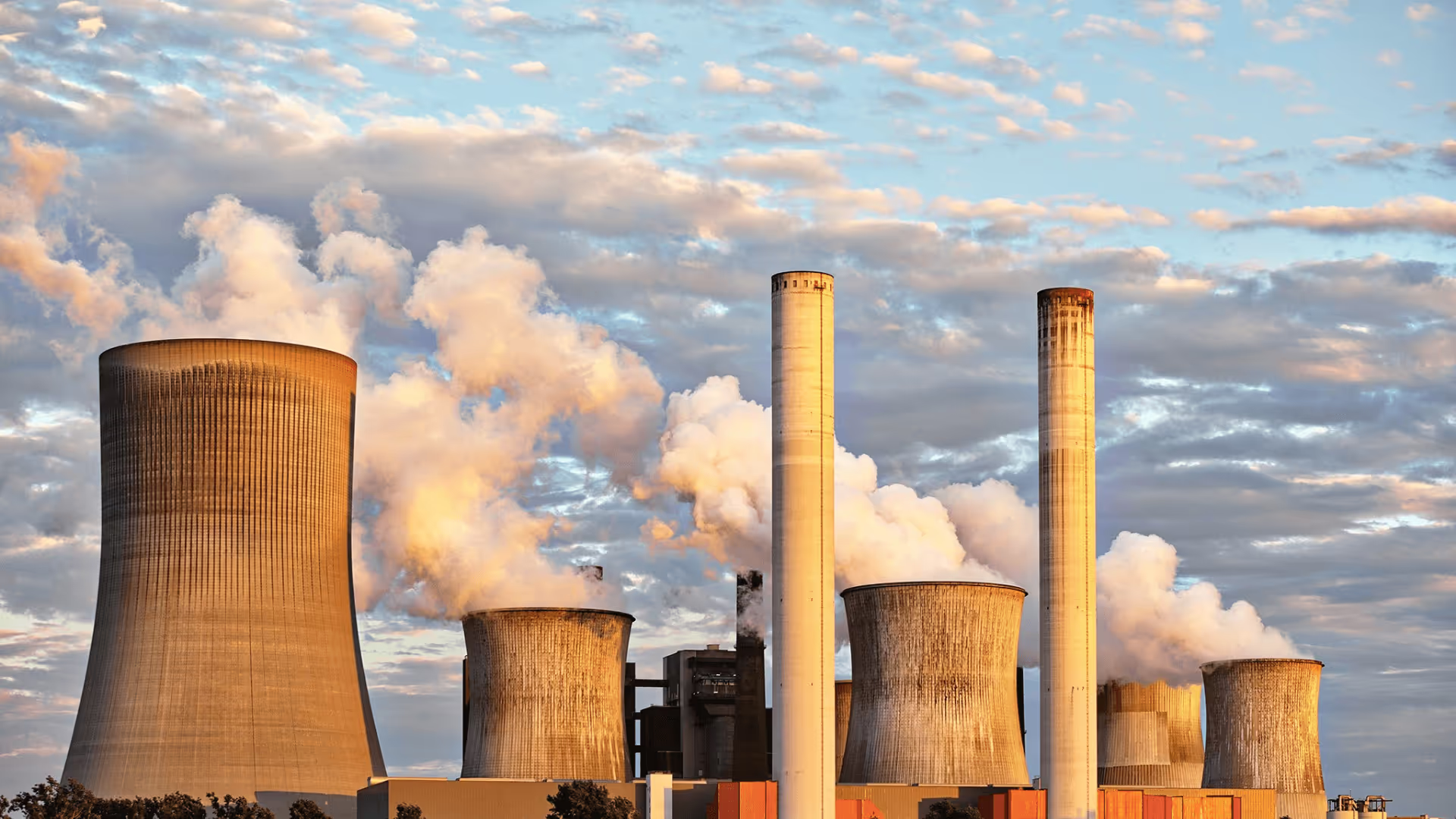
Why MRO Supply Chains Matter for Coal-Fired Energy in ANZ in 2025
Coal-fired power stations remain a significant part of ANZ’s energy mix, despite the global shift toward renewables. In Australia, coal generates about 50% of electricity, while in New Zealand, it supports peak demand. However, the age of these assets—many built in the mid-20th century—combined with high levels of unplanned, reactive maintenance, drives up costs and risks outages. For Government bodies overseeing energy policy and providers like AGL or Genesis Energy, an efficient MRO supply chain is essential to manage these challenges.
The ANZ Energy Context
In 2025, ANZ faces rising energy demands, aging infrastructure, and pressure to transition to cleaner energy. Coal-fired plants, with their outdated equipment, are particularly vulnerable to breakdowns, leading to costly reactive repairs and supply chain inefficiencies. Optimising MRO processes can help balance reliability, cost control, and sustainability goals.
Key Challenges in MRO Supply Chains for Coal-Fired Energy
The high costs in coal-fired energy MRO supply chains stem from two major issues: old assets and unplanned, reactive maintenance. Let’s break them down.
1. The Burden of Old Assets: Aging Infrastructure Drives Costs
The Age Factor
Many coal-fired power stations in ANZ, such as Australia’s Liddell Power Station (set to close in 2023 but reflective of the sector’s age profile) or New Zealand’s Huntly Power Station, are decades old. Components like turbines, boilers, and conveyors wear out faster, requiring frequent repairs or replacements.
Cost Implications
- Higher Repair Costs: Aging parts are expensive to fix or source, often requiring custom fabrication.
- Downtime Risks: Older assets are prone to unexpected failures, halting production and increasing lost revenue.
- Obsolescence: Spare parts for legacy equipment are harder to find, driving up procurement costs.
Strategies to Address Old Assets
- Asset Assessment: Regularly evaluate equipment condition to prioritise maintenance or replacement.
- Lifecycle Planning: Develop long-term plans to phase out obsolete assets or upgrade critical components.
- Preventive Maintenance: Shift from reactive to proactive care to extend asset life.
How Trace Consultants Can Help
Trace Consultants will conduct comprehensive asset assessments to identify high-risk components. We’ll design lifecycle plans and implement preventive maintenance strategies, helping you manage old assets efficiently and reduce long-term costs.
2. High Levels of Unplanned, Reactive Maintenance: A Costly Cycle
The Reactive Trap
Unplanned, reactive maintenance—fixing equipment only after it breaks—dominates coal-fired energy operations in ANZ. This approach leads to emergency repairs, rushed spare part orders, and production delays, particularly during peak demand periods.
Cost and Reliability Impacts
- Emergency Expenses: Reactive fixes often cost more due to overtime labour and expedited shipping.
- Supply Chain Strain: Sudden demand for parts disrupts MRO supply chains, increasing lead times.
- Outage Risks: Unexpected downtime threatens energy supply, impacting consumers and regulators.
Strategies to Reduce Reactive Maintenance
- Predictive Maintenance: Use sensors and data analytics to predict failures before they occur.
- Inventory Management: Maintain strategic stock of critical spares to avoid delays.
- Maintenance Scheduling: Plan outages during low-demand periods to minimise disruption.
How Trace Consultants Can Help
Trace Consultants will introduce predictive maintenance systems and optimise your inventory management. We’ll develop scheduling plans tailored to ANZ’s energy demand cycles, reducing reactive maintenance and its associated costs.
Key Strategies for Optimising MRO Supply Chains
To address the challenges of old assets and reactive maintenance, ANZ Government and Energy Providers can adopt these strategies.
1. Transitioning to Predictive Maintenance: Leveraging Technology
The Power of Prediction
Predictive maintenance uses IoT sensors, machine learning, and real-time data to monitor equipment health, predicting failures before they happen. For coal-fired plants, this can track turbine vibrations or boiler pressure, enabling timely interventions.
ANZ Benefits
In ANZ, where coal plants are spread across remote areas (e.g., Queensland’s coal regions), predictive tools reduce travel costs for technicians and minimise downtime, aligning with government reliability goals.
How Trace Consultants Can Help
Trace Consultants will implement predictive maintenance solutions, integrating IoT and analytics into your MRO supply chain. Our expertise ensures your coal-fired assets are monitored effectively, cutting unplanned outages.
2. Optimising Inventory and Procurement: Streamlining Supplies
Inventory Challenges
Coal-fired energy relies on a complex array of spares—valves, bearings, and control systems—often with long lead times. Poor inventory management exacerbates reactive maintenance costs.
Strategies for Improvement
- Strategic Stocking: Pre-position critical spares near high-risk plants.
- Vendor Partnerships: Build long-term agreements with reliable suppliers.
- Demand Forecasting: Use historical data to predict spare part needs.
How Trace Consultants Can Help
Trace Consultants will optimise your inventory strategy, negotiating with vendors and forecasting demand to ensure spares are available when needed. Our approach reduces procurement costs and lead times.
3. Enhancing Supply Chain Visibility: One Source of Truth
The Visibility Gap
Lack of visibility into MRO supply chains—e.g., part locations or order statuses—leads to inefficiencies. Government and energy providers need a unified view to coordinate maintenance across multiple sites.
Strategies for Visibility
- Integrated Systems: Use ERP or MRO-specific software to track parts and processes.
- Real-Time Dashboards: Provide managers with live updates on stock and maintenance.
- Cross-Department Collaboration: Align operations, procurement, and maintenance teams.
How Trace Consultants Can Help
Trace Consultants will implement integrated systems and real-time dashboards for your MRO supply chain. We’ll foster collaboration across departments, ensuring a single source of truth to drive efficiency.
4. Workforce Upskilling: Building Maintenance Capability
The Skills Shortage
ANZ’s energy sector faces a skills gap, with fewer technicians trained to maintain aging coal-fired assets. This reliance on external contractors increases costs and delays.
Strategies for Upskilling
- Training Programs: Develop in-house skills for predictive maintenance and equipment repair.
- Knowledge Transfer: Document expertise from retiring workers to train new staff.
- Certification Support: Partner with technical institutes for ongoing education.
How Trace Consultants Can Help
Trace Consultants will design workforce upskilling programs, focusing on predictive maintenance and equipment management. We’ll support knowledge transfer and certification, building your internal capability.
Broader Impacts and Opportunities in 2025
Optimising MRO supply chains offers more than cost savings—it aligns with broader goals for ANZ’s energy sector.
1. Supporting the Energy Transition
Balancing Coal and Renewables
While coal-fired energy remains vital, ANZ is transitioning to renewables. Optimised MRO can extend the life of coal assets during this shift, allowing time to build renewable capacity without compromising supply.
Opportunities
- Cost Deferral: Delay expensive plant replacements with better maintenance.
- Regulatory Compliance: Meet government emission targets with efficient operations.
How Trace Consultants Can Help
Trace Consultants will align your MRO optimisation with the energy transition, designing strategies that defer costs and ensure compliance with ANZ regulations.
2. Improving Reliability and Public Trust
Reliability Matters
Unplanned outages erode public trust in energy providers. A robust MRO supply chain reduces downtime, ensuring stable power for homes and businesses across ANZ.
Opportunities
- Enhanced Reputation: Consistent supply builds consumer confidence.
- Government Support: Reliable operations strengthen funding cases for upgrades.
How Trace Consultants Can Help
Trace Consultants will enhance your reliability through MRO optimisation, improving public trust and supporting your case for government backing.
Challenges of Optimising MRO Supply Chains
Optimising MRO supply chains in coal-fired energy comes with hurdles:
1. Budget Constraints
High initial costs for technology or training strain government and provider budgets.
2. Legacy Systems
Old IT infrastructure complicates integration with modern MRO tools.
3. Resistance to Change
Staff may resist shifting from reactive to predictive maintenance.
4. Supply Chain Complexity
Global supply issues for coal plant spares add procurement risks.
These challenges are manageable with strategic planning.
Opportunities with Optimised MRO Supply Chains in 2025
An optimised MRO supply chain offers ANZ Government and Energy Providers:
- Cost Reduction: Lower repair and downtime costs with predictive maintenance.
- Improved Reliability: Reduce outages with better asset management.
- Sustainability Support: Extend asset life during the transition to renewables.
- Workforce Efficiency: Upskill staff to reduce reliance on contractors.
In 2025, this is your path to a more efficient energy sector.
How Trace Consultants Can Help ANZ Government and Energy Providers
At Trace Consultants, we bring deep expertise to ANZ’s energy MRO supply chains. Here’s how we can help:
1. Asset Assessment and Lifecycle Planning
We’ll evaluate your coal-fired assets, identifying risks and designing lifecycle plans to manage aging infrastructure.
2. Predictive Maintenance Implementation
We’ll introduce IoT and analytics to shift from reactive to predictive maintenance, reducing unplanned outages.
3. Inventory and Procurement Optimisation
We’ll streamline your spare parts inventory, negotiate vendor partnerships, and forecast demand to cut costs.
4. Supply Chain Visibility Solutions
We’ll implement integrated systems and real-time dashboards, ensuring a single source of truth across your operations.
5. Workforce Upskilling Programs
We’ll develop training and knowledge transfer initiatives to build internal maintenance capability.
6. Transition Support
We’ll align your MRO strategy with the energy transition, deferring costs and ensuring regulatory compliance.
7. Reliability Enhancement
We’ll optimise your MRO processes to improve reliability, boosting public trust and government support.
8. Ongoing Support and Strategy Refinement
We’ll provide continuous support, refining your MRO supply chain to adapt to ANZ’s evolving energy needs.
We work hands-on, partnering with you to transform your MRO supply chain. With Trace Consultants, your coal-fired energy operations will be more efficient, reliable, and future-ready.
Looking Ahead: Your MRO Advantage in 2025
In 2025, optimising MRO supply chains is how ANZ Government and Energy Providers manage the high costs of coal-fired energy. Tackling old assets with lifecycle planning and reducing unplanned maintenance through predictive tools and better inventory management will drive efficiency. Supporting the energy transition, improving reliability, and upskilling your workforce will ensure long-term success.
Don’t let outdated practices drain your resources. Contact Trace Consultants today. Let’s optimise your MRO supply chain—because in ANZ’s energy sector, every dollar and minute counts.
Ready to turn insight into action?
We help organisations transform ideas into measurable results with strategies that work in the real world. Let’s talk about how we can solve your most complex supply chain challenges.